Machining method of motor stator core
A motor stator and processing method technology, which is applied in the manufacture of motor generators, electrical components, electromechanical devices, etc., can solve the problems affecting the performance of the motor stator core, and the electrical steel sheet is easy to rust, so as to ensure performance and reduce the influence of magnetic properties , cost reduction effect
- Summary
- Abstract
- Description
- Claims
- Application Information
AI Technical Summary
Problems solved by technology
Method used
Image
Examples
Embodiment Construction
[0019] see figure 1 , a method for processing a motor stator core provided by an embodiment of the present invention includes:
[0020] Step S1, dipping and dripping paint on a plurality of electrical steel laminations.
[0021] Step S2, performing hot pressing on a plurality of electrical steel laminations to obtain electrical steel laminations.
[0022] Step S3, drilling and wire-cutting the electrical steel stack to obtain the stator core block.
[0023] Step S4, performing laser welding on the stator core block to obtain the stator core.
[0024] Specific Embodiments of the Application Due to the dipping and dripping of multiple electrical steel laminations, a paint film is formed on the surface of the electrical steel laminations to protect the electrical steel laminations, avoid corrosion, and ensure the performance of the motor stator core , because multiple electrical steel laminations are hot-pressed to obtain electrical steel lamination blocks, so there is no need...
PUM
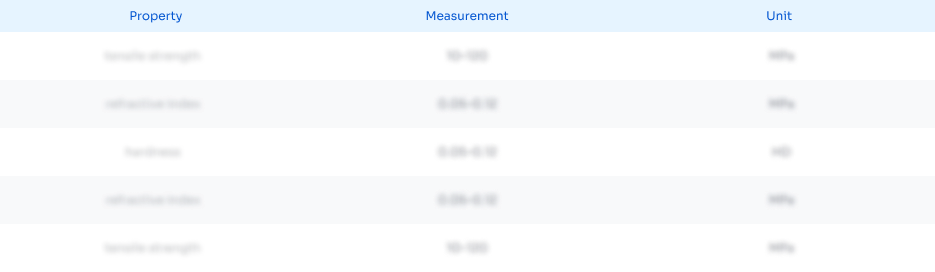
Abstract
Description
Claims
Application Information

- R&D Engineer
- R&D Manager
- IP Professional
- Industry Leading Data Capabilities
- Powerful AI technology
- Patent DNA Extraction
Browse by: Latest US Patents, China's latest patents, Technical Efficacy Thesaurus, Application Domain, Technology Topic.
© 2024 PatSnap. All rights reserved.Legal|Privacy policy|Modern Slavery Act Transparency Statement|Sitemap