Shaft hole centering guide method in workpiece assembly process based on machine vision
An assembly process and machine vision technology, applied in manipulators, manufacturing tools, program-controlled manipulators, etc., can solve problems such as the inability to effectively complete the assembly process, face fixed scenes, and fail to complete pre-selected tasks well.
- Summary
- Abstract
- Description
- Claims
- Application Information
AI Technical Summary
Problems solved by technology
Method used
Image
Examples
Embodiment Construction
[0024] The following are specific implementation cases of the present invention and in conjunction with the accompanying drawings, further describe the technical solution of the present invention, but the present invention is not limited to these implementation cases.
[0025] It should also be understood that the specific embodiments described here are only for understanding the present invention, and are not intended to limit the present invention.
[0026] The target image processed by the present invention comes from the industrial camera of the industrial robot, and the industrial camera is used to detect workpieces on the production line.
[0027] like figure 1 As shown, the step-by-step operation of a vision-based workpiece detection method proposed by the present invention is as follows:
[0028] Step 1. The model diagram of the bolt (M12) to be identified and matched (assembled) is used as a 3D object model. When creating the bolt model, the central axis of the bolt ...
PUM
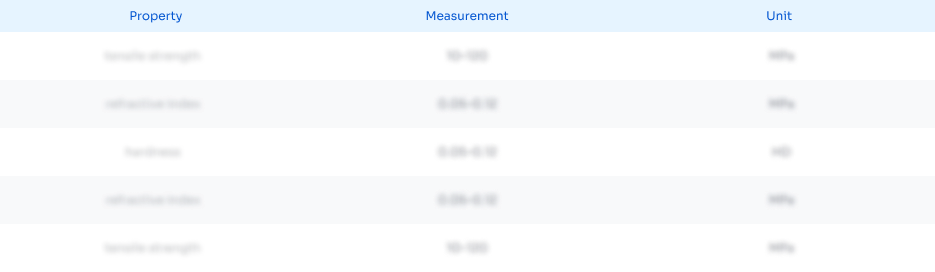
Abstract
Description
Claims
Application Information

- R&D Engineer
- R&D Manager
- IP Professional
- Industry Leading Data Capabilities
- Powerful AI technology
- Patent DNA Extraction
Browse by: Latest US Patents, China's latest patents, Technical Efficacy Thesaurus, Application Domain, Technology Topic, Popular Technical Reports.
© 2024 PatSnap. All rights reserved.Legal|Privacy policy|Modern Slavery Act Transparency Statement|Sitemap|About US| Contact US: help@patsnap.com