Multi-step inner hole machining method
A processing method and multi-step technology, applied in the field of gearboxes, can solve the problems that the machining accuracy of the multi-step inner hole structure cannot be guaranteed, the consistency of the finished product is poor, and the coaxiality is difficult to ensure, so as to improve the quality of the valve control surface and the high yield. , the effect of high processing efficiency
- Summary
- Abstract
- Description
- Claims
- Application Information
AI Technical Summary
Problems solved by technology
Method used
Image
Examples
Embodiment 1
[0028] This embodiment provides a multi-step inner hole processing method, including the following steps:
[0029] 1) Design the tool according to the structure of the multi-step inner hole 4 to be processed. Wherein, the tool includes a clamping rod 1 and a reamer rod 2 . The tool is provided with a through cooling hole 3 along the length direction. A liquid outlet hole 206 is also arranged on the body of the reamer rod 2 . The liquid outlet hole 206 communicates with the cooling hole 3 and the outside of the reamer rod 2 . The reamer rod 2 includes a first reamer head 201 , a second reamer head 202 , a third reamer head 203 and a fourth reamer head 204 arranged coaxially in sequence along a direction away from the clamping rod 1 . The first reamer head 201 , the second reamer head 202 , the third reamer head 203 and the fourth reamer head 204 are cylinders whose diameters decrease successively as a whole. The outer walls of the first reamer head 201 , the second reamer h...
Embodiment 2
[0038] This embodiment provides a basic multi-step inner hole processing method, including the following steps:
[0039] 1) Design the tool according to the structure of the multi-step inner hole 4 to be processed. Wherein, the tool includes a clamping rod 1 and a reamer rod 2 . The tool is provided with a through cooling hole 3 along the length direction. The reamer rod 2 includes a first reamer head 201 , a second reamer head 202 , a third reamer head 203 and a fourth reamer head 204 arranged coaxially in sequence along a direction away from the clamping rod 1 . The first reamer head 201 , the second reamer head 202 , the third reamer head 203 and the fourth reamer head 204 are cylinders whose diameters decrease successively as a whole. The outer walls of the first reamer head 201 , the second reamer head 202 , the third reamer head 203 and the fourth reamer head 204 are provided with cutting edges 205 with unequal tooth distribution. The fourth reamer head 204 defines a ...
Embodiment 3
[0046] The main steps of this embodiment are the same as those of Embodiment 2, wherein the outer wall of the clamping rod 1 is a smooth surface. The outer wall of the reamer rod 2 is covered with superhard abrasives. The grain sizes of the first reamer head 201 , the second reamer head 202 , the third reamer head 203 and the fourth reamer head 204 are different.
PUM
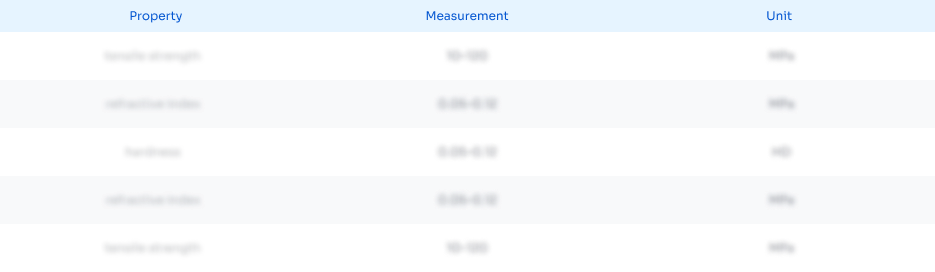
Abstract
Description
Claims
Application Information

- R&D
- Intellectual Property
- Life Sciences
- Materials
- Tech Scout
- Unparalleled Data Quality
- Higher Quality Content
- 60% Fewer Hallucinations
Browse by: Latest US Patents, China's latest patents, Technical Efficacy Thesaurus, Application Domain, Technology Topic, Popular Technical Reports.
© 2025 PatSnap. All rights reserved.Legal|Privacy policy|Modern Slavery Act Transparency Statement|Sitemap|About US| Contact US: help@patsnap.com