Pvd thickness control
A technology of coating thickness and speed, which is applied to metal substrates, especially the field of coating metal strips with zinc, can solve problems such as slow atomization rate, no coating thickness, and non-compliance with quality requirements.
- Summary
- Abstract
- Description
- Claims
- Application Information
AI Technical Summary
Problems solved by technology
Method used
Image
Examples
Embodiment Construction
[0033] exist figure 1 An embodiment variant of the device 1 according to the invention is shown schematically in a very simplified side view.
[0034] The plant 1 is suitable for carrying out the method according to the invention, in which a metal strip 10 is treated with a metal substrate 12 according to the principle of physical vapor deposition (PVD), wherein, through the parameters of strip speed and atomization rate, Adjust the coating thickness according to the formula below.
[0035]
[0036] in:
[0037]
[0038]
[0039]The plant 1 firstly comprises a continuous processing line 2 in which the metal strip 10 is first uncoiled by a first coiling device 11 and then recoiled at the end of the processing line 2 by a second coiling device 13 . Inside the processing line 2 the metal strip 10 is moved in the direction of movement of the arrow 3 and in this case passed through a plurality of stations.
[0040] In the embodiment variant described here, the plant 1 ...
PUM
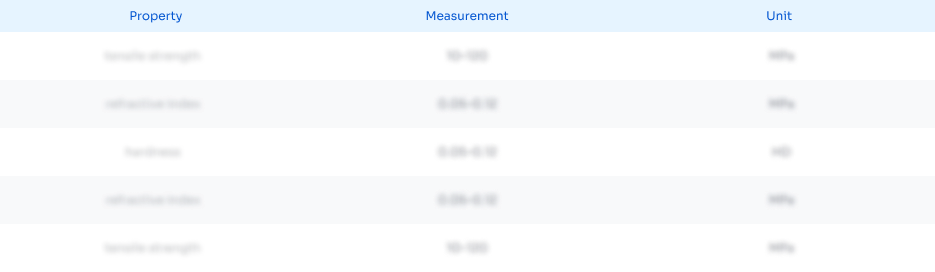
Abstract
Description
Claims
Application Information

- R&D
- Intellectual Property
- Life Sciences
- Materials
- Tech Scout
- Unparalleled Data Quality
- Higher Quality Content
- 60% Fewer Hallucinations
Browse by: Latest US Patents, China's latest patents, Technical Efficacy Thesaurus, Application Domain, Technology Topic, Popular Technical Reports.
© 2025 PatSnap. All rights reserved.Legal|Privacy policy|Modern Slavery Act Transparency Statement|Sitemap|About US| Contact US: help@patsnap.com