Method for recovering organic tin acetate from waste floccules in sucralose production
A technology of sucralose and floc, which is applied in the field of recycling organotin acetate, can solve the problems of high energy consumption, poor catalytic efficiency, and low purity of DSDA recovery, and achieve good effect, stable production efficiency, and alkali hydrolysis effect Good results
- Summary
- Abstract
- Description
- Claims
- Application Information
AI Technical Summary
Problems solved by technology
Method used
Examples
Embodiment 1
[0017] a. Add 1,000ml of the waste floc aqueous solution obtained by layering treatment after the esterification reaction into a single-necked flask for heating and vacuum distillation, control the temperature at 100°C, and the distillation pressure at -0.09MPa, and distill off water and cyclohexane, etc. Volatile impurities were obtained to obtain 238g of black tar;
[0018] b. Weigh 200g of the dark brown tarry substance obtained in step a and mix it with 200ml of methanol to dissolve, and the dissolution temperature is normal temperature (25°C);
[0019] c. Configure 500ml of sodium hydroxide solution with a concentration of 5%, raise the temperature to 80°C, slowly add the mixed dark brown floc into the NaOH solution, and control the neutralization temperature at about 80°C. Stir for 2 hours, filter with a Buchner funnel, and wash with hot water until the washing water is colorless, dry the obtained dibutyltin oxide in an oven at 60°C for 12 hours, and obtain white dibutyl...
Embodiment 2
[0024] a. Add 1,000ml of the waste floc aqueous solution obtained by layering treatment after the esterification reaction into a single-necked flask for heating and vacuum distillation. The temperature is controlled at 90°C, and the distillation pressure is -0.09MPa. Water and cyclohexane, etc. are distilled off. Volatile impurities were obtained to obtain 226g of black tar;
[0025] b. Weigh 200g of the dark brown tarry substance obtained in step a and mix it with 300ml of ethanol to dissolve, and the dissolution temperature is normal temperature (25°C);
[0026] c. Configure 500ml of sodium hydroxide solution with a concentration of 5%, raise the temperature to 80°C, slowly add the mixed dark brown floc into the NaOH solution, and control the neutralization temperature at about 80°C. Stir for 2 hours, filter with a Buchner funnel, and wash with hot water until the washing water is colorless, dry the obtained dibutyltin oxide in an oven at 80°C for 5 hours, and obtain white d...
Embodiment 3
[0031] a. Add 1,000ml of the waste floc aqueous solution obtained by layering treatment after the esterification reaction into a single-necked flask for heating and vacuum distillation. The temperature is controlled at 95°C, the distillation pressure is -0.09MPa, and water and cyclohexane are removed by distillation. Volatile impurities were obtained to obtain 229g of black tar;
[0032] b. Weigh 200g of the dark brown tarry substance obtained in step a and mix it with 500ml of acetone to dissolve, and the dissolution temperature is normal temperature (25°C);
[0033] c. Configure 500ml of sodium hydroxide solution with a concentration of 5%, raise the temperature to 85°C, slowly add the mixed dark brown floc into the NaOH solution, and control the neutralization temperature at about 85°C. Stir for 2 hours, filter with a Buchner funnel, and wash with hot water until the washing water is colorless, dry the obtained dibutyltin oxide in an oven at 85°C for 6 hours, and obtain whi...
PUM
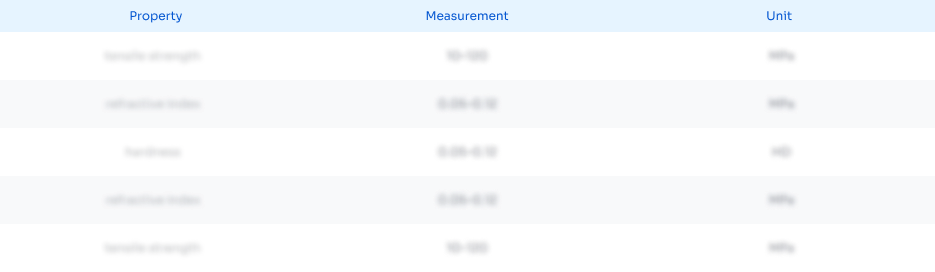
Abstract
Description
Claims
Application Information

- Generate Ideas
- Intellectual Property
- Life Sciences
- Materials
- Tech Scout
- Unparalleled Data Quality
- Higher Quality Content
- 60% Fewer Hallucinations
Browse by: Latest US Patents, China's latest patents, Technical Efficacy Thesaurus, Application Domain, Technology Topic, Popular Technical Reports.
© 2025 PatSnap. All rights reserved.Legal|Privacy policy|Modern Slavery Act Transparency Statement|Sitemap|About US| Contact US: help@patsnap.com