Redox preparation process of an oxygen carrier for a chemical looping process
A technology of oxygen carrier and chemical chain, applied in the direction of physical/chemical process catalysts, chemical instruments and methods, chemical/physical processes, etc., can solve the problems of oxygen carrier materials, energy density, and expensive
- Summary
- Abstract
- Description
- Claims
- Application Information
AI Technical Summary
Problems solved by technology
Method used
Image
Examples
Embodiment 1
[0108] by containing 20 vol% H at a temperature of 850°C 2 The oxygen carrier material was reduced overnight in He flow (100 seem) to obtain pre-reduced oxygen carrier material.
[0109] 0.76g CuCl 2 .2H 2 O dissolved in 1.1ml H 2 O, thus obtaining 4.05M Cu 2+ solution. 0.050 g of this solution was contacted with 0.5072 g of pre-reduced oxygen carrier (OC) material. In the case of a quantitative reaction, 0.013 g of Cu could be deposited. The observed final Fe:Cu molar ratio was 36.1:1.
Embodiment 2
[0111] 0.0241g CuCl 2 .2H 2 O dissolved in 0.4993g H 2 O, thus obtaining 0.283M Cu 2+ solution.
[0112] 0.30 g of this solution was contacted with 1 g of pre-reduced oxygen carrier material obtained by heating at 900° C. 2 Obtained by overnight reduction in He (100 sccm). 0.0054 g Cu could be deposited in case of quantitative reaction. The Fe:Cu molar ratio in the final product obtained was observed to be 87:1.
Embodiment 3
[0114] 0.4614g CuCl 2 .2H 2 O dissolved in 0.5058g H 2 O, thus obtaining 5.35M in H 2 solution in O. 0.30 g of this solution was contacted overnight with 1 g of pre-reduced oxygen carrier material produced by heating at 900° C. 2 obtained by reducing the oxygen carrier material in the presence of flowing He (100 sccm).
[0115] In case of quantitative reaction, 0.102 g Cu can be deposited on the oxygen carrier material. A final Fe:Cu molar ratio of 3.7:1 was obtained
[0116] SEM & Optical Microscopy
[0117] On polished cross-sections of embedded particles inside epoxy resin, the concentration of oxygen carriers was studied by optical microscopy (SteREO imager, ZEISS) and by scanning electron microscopy using a FEI NOVA Nanosem 450 with an energy dispersive spectrometer (EDS) system. microstructure.
PUM
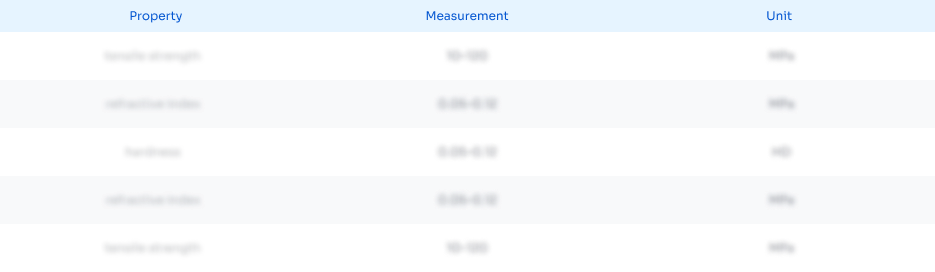
Abstract
Description
Claims
Application Information

- R&D
- Intellectual Property
- Life Sciences
- Materials
- Tech Scout
- Unparalleled Data Quality
- Higher Quality Content
- 60% Fewer Hallucinations
Browse by: Latest US Patents, China's latest patents, Technical Efficacy Thesaurus, Application Domain, Technology Topic, Popular Technical Reports.
© 2025 PatSnap. All rights reserved.Legal|Privacy policy|Modern Slavery Act Transparency Statement|Sitemap|About US| Contact US: help@patsnap.com