Method for forming oxide layer
An oxide layer and oxidizing technology, applied in the field of solar cells, can solve the problem of the need to further improve the compactness of the oxide layer, and achieve the effects of excellent thickness and compactness, low attenuation value, and good internal and external consistency
- Summary
- Abstract
- Description
- Claims
- Application Information
AI Technical Summary
Problems solved by technology
Method used
Image
Examples
Embodiment 1
[0062] This embodiment forms the oxide layer according to the following method:
[0063] 1) Into the boat (put the silicon wafer used for solar cells in the quartz boat first, and then put the quartz boat in the reactor): temperature 600°C, nitrogen gas 15000sccm, pressure 1060mbar, time 700s;
[0064] 2) Heating: temperature 700°C, nitrogen flow 15000sccm, pressure 1060mbar, time 500s;
[0065] 3) Vacuuming: temperature 700°C, pressure 0, time 200s;
[0066] 4) Oxidation: temperature 700°C, pressure 300mbar, oxygen 1000sccm, time 1200s;
[0067] 5) Vacuuming: the temperature is 700°C, the pressure is 0, and the time is 200s;
[0068] 6) Back pressure: temperature 600°C, nitrogen flow 15000sccm, pressure 1060mbar, time 90s;
[0069] 7) Cooling: 600°C, 15000sccm nitrogen flow, 1060mbar pressure, 300s time;
[0070] 8) Out of the boat (take out the quartz boat and the silicon wafer with the oxide layer): blow nitrogen gas at 15000 sccm for 700 s.
Embodiment 2
[0072] This embodiment forms the oxide layer according to the following method:
[0073] 1) Into the boat (put the silicon wafer used for solar cells in the quartz boat first, and then put the quartz boat in the reactor): temperature 600°C, nitrogen gas 15000sccm, pressure 1060mbar, time 700s;
[0074] 2) Heating: temperature 700°C, nitrogen flow 15000sccm, pressure 1060mbar, time 500s;
[0075] 3) Vacuuming: temperature 700°C, pressure 0, time 200s;
[0076] 4) Oxidation: temperature 700°C, pressure 500mbar, oxygen 1000sccm, time 1200s;
[0077] 5) Vacuuming: the temperature is 700°C, the pressure is 0, and the time is 200s;
[0078] 6) Back pressure: temperature 600°C, nitrogen flow 15000sccm, pressure 1060mbar, time 90s;
[0079] 7) Cooling: 600°C, 15000sccm nitrogen flow, 1060mbar pressure, 300s time;
[0080] 8) Out of the boat (take out the quartz boat and the silicon wafer with the oxide layer): blow nitrogen gas at 15000 sccm for 700 s.
Embodiment 3
[0082] This embodiment forms the oxide layer according to the following method:
[0083] 1) Into the boat (put the silicon wafer used for solar cells in the quartz boat first, and then put the quartz boat in the reactor): temperature 600°C, nitrogen gas 15000sccm, pressure 1060mbar, time 700s;
[0084] 2) Heating: temperature 700°C, nitrogen flow 15000sccm, pressure 1060mbar, time 500s;
[0085] 3) Vacuuming: temperature 700°C, pressure 0, time 200s;
[0086] 4) Oxidation: temperature 700°C, pressure 800mbar, oxygen 1000sccm, time 1200s;
[0087] 5) Vacuuming: the temperature is 700°C, the pressure is 0, and the time is 200s;
[0088] 6) Back pressure: temperature 600°C, nitrogen flow 15000sccm, pressure 1060mbar, time 90s;
[0089] 7) Cooling: 600°C, 15000sccm nitrogen flow, 1060mbar pressure, 300s time;
[0090] 8) Out of the boat (take out the quartz boat and the silicon wafer with the oxide layer): blow nitrogen gas at 15000 sccm for 700 s.
PUM
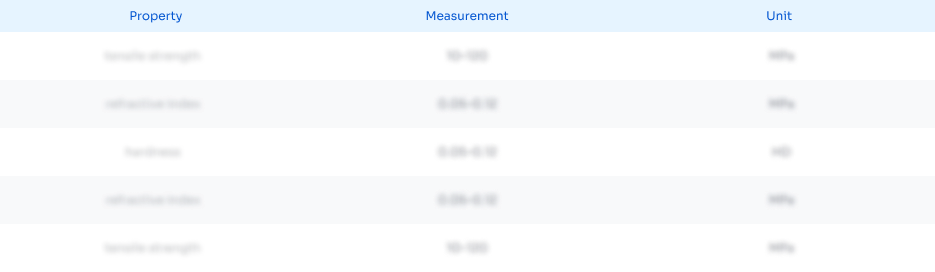
Abstract
Description
Claims
Application Information

- R&D
- Intellectual Property
- Life Sciences
- Materials
- Tech Scout
- Unparalleled Data Quality
- Higher Quality Content
- 60% Fewer Hallucinations
Browse by: Latest US Patents, China's latest patents, Technical Efficacy Thesaurus, Application Domain, Technology Topic, Popular Technical Reports.
© 2025 PatSnap. All rights reserved.Legal|Privacy policy|Modern Slavery Act Transparency Statement|Sitemap|About US| Contact US: help@patsnap.com