High-performance easy-to-forge magnesium alloy material and preparation method thereof
A magnesium alloy, high-performance technology, applied in the field of high-performance and easy-forging magnesium alloy materials and preparation, can solve the problems of low strength, large distance, poor plastic deformation ability, etc., and achieve the effect of improving high temperature strength and creep resistance
- Summary
- Abstract
- Description
- Claims
- Application Information
AI Technical Summary
Problems solved by technology
Method used
Examples
Embodiment 1
[0025] The high performance of the present invention includes the following composition: Magnesium elements: marginality, Y element: 7.5%, CD element: 0.6%, CE / LA element: 3.5%.
[0026] The preparation method is as follows:
[0027] 1) Follow the above-mentioned mating ratio, melting into a ingot, the smelting process is as follows: In the furnace passing into the protective gas: sf 6 + CO 2 The SF6 volume ratio is: 0.7%, the rest is CO 2 After the heating power is 15kW, after 13 minutes, heating power 25 kW is heated to the solution melt, and then heats up for 25 minutes during heating power, and then cools the heating power 12 kW to the cast temperature, cast temperature: 720 ° C, then pouring;
[0028] 2) ingot annealing: homogenization treatment of ingots: homogenization temperature: 380 ° C, time: 10h; water quenching;
[0029] 3) Forging:
[0030] Ingot heating time and temperature: 300mm in diameter, ingot heating temperature 380 ° C, to warm post-warm post-holding time;...
Embodiment 2
[0038] The high performance of the present invention comprises the following composition: Magnesium elements: marginality, Y element: 8.5%, CD element: 1.0%, CE / LA element: 3.6%.
[0039] The preparation method is as follows:
[0040] 1) Follow the above-mentioned mating ratio, melting into a ingot, the smelting process is as follows: In the furnace passing into the protective gas: sf 6 + CO 2 The SF6 volume ratio is: 0.9%, the rest is CO 2 After the heating power is 18 kW, the heating power is 30 kW heating to the solution melt, and then heats up for 30 minutes in the heating power, then the heating power is 18 kW to cool down for 20 minutes to the casting temperature, cast temperature: 730 ° C, then pouring;
[0041] 2) Annex annealing:
[0042] Homogenization treatment for ingots: homogenization temperature: 390 ° C, time: 10h; water quenching;
[0043] 3) Forging:
[0044] Ingot heating time and temperature: 300mm in diameter ingot heating temperature 390 ° C, to warm post-w...
Embodiment 3
[0052] The high performance of the present invention comprises the following composition: Magnesium element: marginality, Y element: 9.5%, CD element: 1.3%, CE / LA element: 3.8%.
[0053] The preparation method is as follows:
[0054] 1) Follow the above-mentioned mating ratio, melting into a ingot, the smelting process is as follows: In the furnace passing into the protective gas: sf 6 + CO 2 The SF6 volume ratio is: 0.3%, the rest is CO 2 After the heating power is 15 kW, after 20 minutes, the heating power is 20 kW heating to the solution melt, then heats up for 25 minutes during heating power, and then cools 10 minutes to the casting temperature, casting temperature: 740 ° C, then pouring;
[0055] 2) Annex annealing:
[0056] Homogenization treatment for ingots: homogenization temperature: 400 ° C, time: 10h; water quenching;
[0057] 3) Forging:
[0058] Ingot heating time and temperature: 300mm in diameter ingot heating temperature 400 ° C, to warm post-thermos, post-therm...
PUM
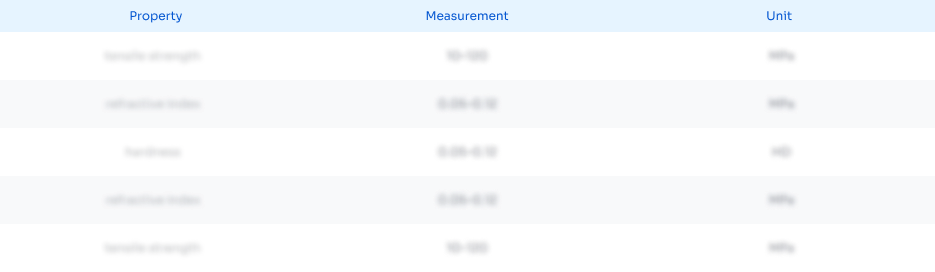
Abstract
Description
Claims
Application Information

- Generate Ideas
- Intellectual Property
- Life Sciences
- Materials
- Tech Scout
- Unparalleled Data Quality
- Higher Quality Content
- 60% Fewer Hallucinations
Browse by: Latest US Patents, China's latest patents, Technical Efficacy Thesaurus, Application Domain, Technology Topic, Popular Technical Reports.
© 2025 PatSnap. All rights reserved.Legal|Privacy policy|Modern Slavery Act Transparency Statement|Sitemap|About US| Contact US: help@patsnap.com