Metal plate polishing thickness detection device for mechanical manufacturing
A thickness detection and mechanical manufacturing technology, applied in the direction of using optical devices, measuring devices, manufacturing tools, etc., can solve problems such as reducing work efficiency and increasing operating procedures, and achieve the effect of improving work efficiency and reducing operating procedures.
- Summary
- Abstract
- Description
- Claims
- Application Information
AI Technical Summary
Problems solved by technology
Method used
Image
Examples
Embodiment
[0041] see Figure 1-5 , a device for measuring the thickness of sheet metal polishing in mechanical manufacturing, comprising a base 1, an operation panel 2 is fixedly connected to the upper end of the base 1, a polisher 3 is fixedly connected to the upper end of the base 1, the polisher 3 is located outside the operation panel 2, and the operation panel 2 The outer end is fixedly connected with a thickness measuring mechanism 4, which is symmetrical to the polisher 3, and a sliding cavity 5 is drilled inside the thickness measuring mechanism 4, and two symmetrical sliding holes 6 are drilled at the outer end of the thickness measuring mechanism 4 , the sliding hole 6 is inserted with a positioning rod 7, the outer end of the positioning rod 7 is fixedly connected with an index 8, the index 8 is slidingly connected with the sliding cavity 5, the outer end of the thickness measuring mechanism 4 is provided with a scale 9, and the scale 9 is located at the position of the index ...
PUM
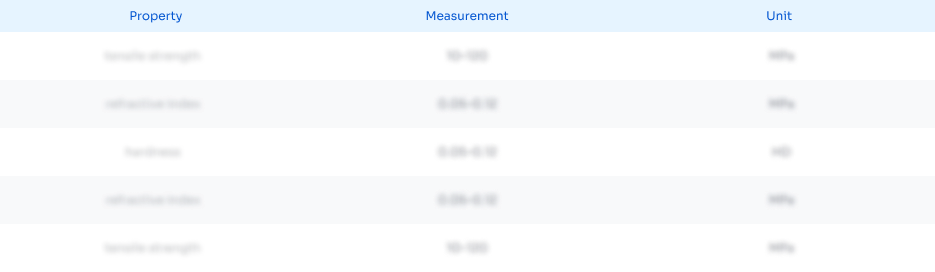
Abstract
Description
Claims
Application Information

- R&D
- Intellectual Property
- Life Sciences
- Materials
- Tech Scout
- Unparalleled Data Quality
- Higher Quality Content
- 60% Fewer Hallucinations
Browse by: Latest US Patents, China's latest patents, Technical Efficacy Thesaurus, Application Domain, Technology Topic, Popular Technical Reports.
© 2025 PatSnap. All rights reserved.Legal|Privacy policy|Modern Slavery Act Transparency Statement|Sitemap|About US| Contact US: help@patsnap.com