Packaging tin raw material tinplate machining treatment system and machining method
A processing system and raw material technology, which is applied in the field of tinplate processing system for raw materials of packaging cans, can solve the problems of processing position error, iron sheet displacement, springback, etc., and achieve the effects of increasing production cost, stabilizing the corrugated shape, and increasing the scope of application
- Summary
- Abstract
- Description
- Claims
- Application Information
AI Technical Summary
Problems solved by technology
Method used
Image
Examples
Embodiment Construction
[0047] The embodiments of the present invention will be described in detail below with reference to the accompanying drawings, but the present invention can be implemented in a variety of different ways of claim defined and covered.
[0048] like Figure 1 to 18 As shown, a packaging tank raw material tubular iron processing system, the system includes a table 10 and a concave groove 101 opened on the top of the table 10, and the left end of the concave groove 101 is concave structure, and the plate 101 on top of the concave groove 101 is Disassembled, after the installed plate and the workbench 10 form each other, the inside of the two vertical sections of the concave groove 101 is provided with a T-type splint 11, and the two T-type splint 11 are in front and rear symmetrical arrangement, T-type splint 11 horizontal segment. The length is larger than the length of the concave groove 101, and the positions of the front and rear ends of the table 10 are located on both sides of the...
PUM
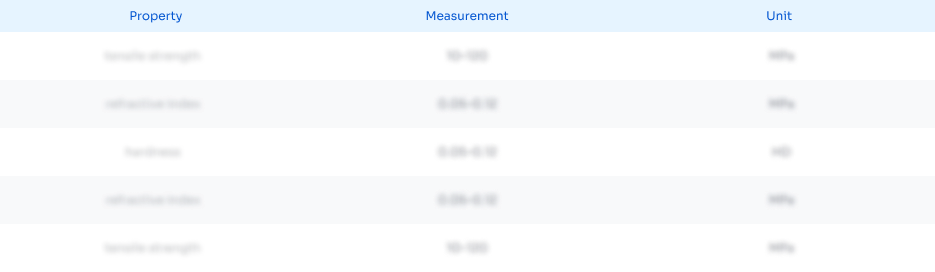
Abstract
Description
Claims
Application Information

- R&D Engineer
- R&D Manager
- IP Professional
- Industry Leading Data Capabilities
- Powerful AI technology
- Patent DNA Extraction
Browse by: Latest US Patents, China's latest patents, Technical Efficacy Thesaurus, Application Domain, Technology Topic, Popular Technical Reports.
© 2024 PatSnap. All rights reserved.Legal|Privacy policy|Modern Slavery Act Transparency Statement|Sitemap|About US| Contact US: help@patsnap.com