Abrasion-resistant coating for front edge of wind power blade and preparation method of abrasion-resistant coating
An anti-corrosion technology for wind turbine blades, applied in coatings, wind power generation, anti-corrosion coatings, etc., can solve problems such as increased maintenance costs, damage to the integrity of wind turbine blades, reduced aerodynamic performance and operational reliability, and achieves improved adhesion , high anti-corrosion performance and adhesion, and convenient construction
- Summary
- Abstract
- Description
- Claims
- Application Information
AI Technical Summary
Problems solved by technology
Method used
Image
Examples
preparation example Construction
[0052] The preparation method of the above-mentioned anti-corrosion coating for the leading edge of wind turbine blades comprises the following steps:
[0053] 1) Prepare the substrate 5. Pre-treat the surface of the leading edge of the blade, which can be polished with sandpaper. After completion, use compressed air to blow for 5 to 10 minutes, decontaminate, degrease and dehumidify, and check the surface quality. There must be no obvious defects on the surface. Defects such as meat, cracks and pits.
[0054] 2) To coat the bottom layer 1, the above-mentioned epoxy paint is evenly stirred, and evenly coated on the surface of the substrate 5 to obtain the bottom layer 1. The coating method of spraying can be used, and the temperature of the surface of the substrate 5 during the coating process is not lower than 10 ℃, the thickness of the bottom layer 1 ranges from 100 to 150um, and it should be properly repaired and polished after curing.
[0055] 3) Coating the middle layer ...
Embodiment 1
[0059] The bottom layer 1 is a two-component solvent-based epoxy coating cured at room temperature.
[0060] The middle layer 2 is an anti-corrosion coating, which is a silicon carbide-reinforced polyurethane-modified epoxy coating, and is composed of components A, B, C and D, and the specific ratio is as shown in the following table Shown:
[0061]
[0062] The dosages of components A, B, C and D are mixed according to the above mass, and the proportioning sequence is as follows: first prepare component A, and then add the uniform mixture of components B and C to group A part, and finally add component D and mix well.
[0063] The leveling layer 3 is made of components B, C, E and F, and the proportioning ratio is shown in the following table:
[0064]
[0065] The dosages of components B, C, E and F are mixed according to the above mass, and the proportioning sequence is: mix components B and C evenly, then add component E, and finally add component F The components...
Embodiment 2
[0074] Compared with Example 1, Example 2 mainly changes the epoxy resin E51 in components A and B to epoxy resin E44, the ratio of other components remains unchanged, and the coating process is the same.
PUM
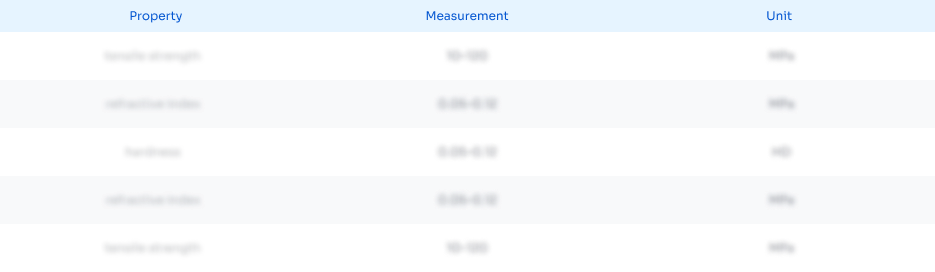
Abstract
Description
Claims
Application Information

- R&D
- Intellectual Property
- Life Sciences
- Materials
- Tech Scout
- Unparalleled Data Quality
- Higher Quality Content
- 60% Fewer Hallucinations
Browse by: Latest US Patents, China's latest patents, Technical Efficacy Thesaurus, Application Domain, Technology Topic, Popular Technical Reports.
© 2025 PatSnap. All rights reserved.Legal|Privacy policy|Modern Slavery Act Transparency Statement|Sitemap|About US| Contact US: help@patsnap.com