Excess material recovery device for rotary kiln
A technology of recovery device and rotary kiln, applied in the field of rotary kiln, can solve the problems of structural damage of rotary kiln, poor thermal conductivity, influence of powder flow rate, etc., and achieve the effect of improving calcination efficiency and restoring thermal conductivity.
- Summary
- Abstract
- Description
- Claims
- Application Information
AI Technical Summary
Problems solved by technology
Method used
Image
Examples
Embodiment Construction
[0024] In order to make the purpose, technical solutions and advantages of the present disclosure clearer, the following in conjunction with specific examples, and refer to Figure 1-3 , to further describe the present disclosure in detail.
[0025] Based on the above purpose, one or more embodiments of this specification provide a rotary kiln residual material recovery device, characterized in that the residual material recovery device is arranged in the rotary kiln body, refer to figure 1 ,include:
[0026] A reciprocating mechanism, one end of the reciprocating mechanism is rotatably connected to the fixture 2 arranged on the inner wall of the smoke exhaust chamber of the rotary kiln; the other end of the reciprocating mechanism is connected to a hydraulic distance increasing mechanism;
[0027] The recovery vehicle is connected with the hydraulic distance-increasing mechanism, and includes a vehicle body 4a and a recovery tank 4b fixed on the vehicle body 4a. A plurality ...
PUM
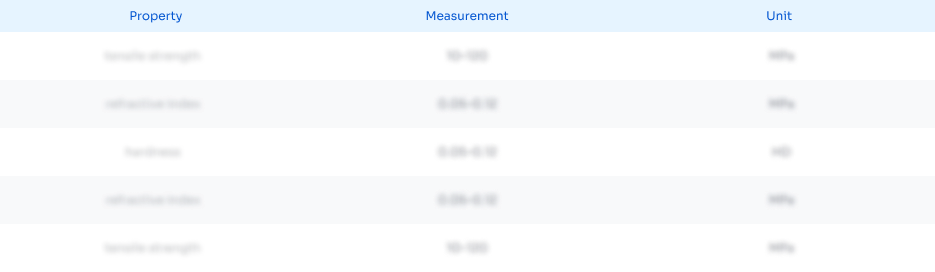
Abstract
Description
Claims
Application Information

- R&D
- Intellectual Property
- Life Sciences
- Materials
- Tech Scout
- Unparalleled Data Quality
- Higher Quality Content
- 60% Fewer Hallucinations
Browse by: Latest US Patents, China's latest patents, Technical Efficacy Thesaurus, Application Domain, Technology Topic, Popular Technical Reports.
© 2025 PatSnap. All rights reserved.Legal|Privacy policy|Modern Slavery Act Transparency Statement|Sitemap|About US| Contact US: help@patsnap.com