High-precision sleeve for electric wire stripping tool and processing technology of high-precision sleeve
A processing technology and high-precision technology, which is applied in the direction of cable installation, disassembly/armoured cable equipment, electrical components, etc., can solve the problems of large force on the sleeve, unfavorable, insufficient precision of the sleeve hole, etc., and reach the limit The effect of improving reliability, improving work efficiency, and reducing the defective rate of slot formation
- Summary
- Abstract
- Description
- Claims
- Application Information
AI Technical Summary
Problems solved by technology
Method used
Image
Examples
Embodiment 1
[0025] like figure 1 A high-precision sleeve for an electric wire stripping tool is shown, including a sleeve body 100, a first sleeve 110, a positioning hole 111, a cable cavity 112, a second sleeve 120, a knife groove seat 121, a cutting Knife 122, chip outlet 123; the first sleeve 110 and the second sleeve 120 are coaxial with the cable cavity 112, integrally formed to form the sleeve body 100; the second sleeve 120 The outer diameter of the first sleeve 110 is larger than that of the first sleeve 110; the positioning hole 111 is provided through the wall of the first sleeve 110; the second sleeve 120 is provided with the knife groove seat 121, so One end of the cutting knife 122 is fixed on the knife groove seat 121, and the cutting knife 122 and the knife groove seat 121 are directly provided with a chip outlet 123 penetrating through the cylinder wall.
[0026] The processing technology of the above-mentioned high-precision sleeve for electric wire stripping tools inclu...
Embodiment 2
[0029] like figure 2 A high-precision sleeve for an electric wire stripping tool is shown, including a sleeve body 100, a first sleeve 110, a positioning hole 111, a cable cavity 112, a second sleeve 120, a knife groove seat 121, a cutting Knife 122, chip outlet 123; the first sleeve 110 and the second sleeve 120 are coaxial with the cable cavity 112, integrally formed to form the sleeve body 100; the second sleeve 120 The outer diameter of the first sleeve 110 is larger than that of the first sleeve 110; the positioning hole 111 is provided through the wall of the first sleeve 110; the second sleeve 120 is provided with the knife groove seat 121, so One end of the cutter 122 is fixed on the knife groove seat 121, and the cutter 122 and the knife groove seat 121 are directly provided with a chip outlet 123 passing through the cylinder wall; preferably, the number of the positioning holes 111 is 2; further, the two positioning holes 111 are on the same plane passing through t...
PUM
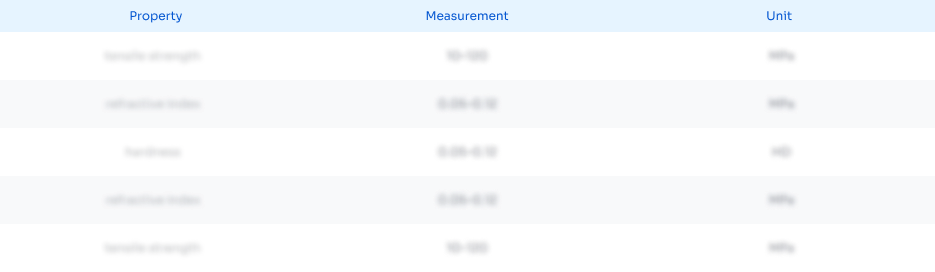
Abstract
Description
Claims
Application Information

- Generate Ideas
- Intellectual Property
- Life Sciences
- Materials
- Tech Scout
- Unparalleled Data Quality
- Higher Quality Content
- 60% Fewer Hallucinations
Browse by: Latest US Patents, China's latest patents, Technical Efficacy Thesaurus, Application Domain, Technology Topic, Popular Technical Reports.
© 2025 PatSnap. All rights reserved.Legal|Privacy policy|Modern Slavery Act Transparency Statement|Sitemap|About US| Contact US: help@patsnap.com