Method for reducing tar adhesion and application thereof
A tar and oleophobic technology, used in coke ovens, petroleum industry, preparation of liquid hydrocarbon mixtures, etc., can solve the problems of acid and alkali corrosion resistance, high temperature resistance, inability to know oleophobic properties, and inability to use tar condensation in high temperature environments. , to achieve the effect of strengthening the oleophobicity of the coating, enhancing the oleophobicity of the coating, and good oleophobicity
- Summary
- Abstract
- Description
- Claims
- Application Information
AI Technical Summary
Problems solved by technology
Method used
Image
Examples
Embodiment 1
[0037] A kind of double-cylinder alternating tar condensation and self-cleaning device, selects the heat exchange tube 18 mainly made of power plant steel and the outer wall of the heat exchange tube 18 is covered with NiCr alloy base oleophobic coating (the Ni of 45wt% and the Cr of 36wt% Doped with 8wt% Mo, 6wt% Fe and 5wt% Si, and using polytetrafluoroethylene-hexafluoropropylene copolymer for surface modification) for tar condensation, the front end is coupled to a reactor made of quartz as the main material For biomass pyrolysis, choose N as the carrier gas 2 , the flue gas temperature is 550°C. In actual application, the pyrolysis gas enters from the pyrolysis gas inlet 17 and flows out from the pyrolysis gas outlet 20, and the condensed working fluid enters from the condensing working fluid inlet 19 and flows out from the condensing working fluid outlet 15, completing the tar condensation work. After multiple pyrolysis, the NiCr alloy coating can reduce the tar adhesio...
Embodiment 2
[0039] A double-cylinder alternating tar condensation and self-cleaning device selects heat exchange tubes 18 made of power plant steel as the main material and the outer wall of the heat exchange tubes 18 is covered with a NiCr alloy-based oleophobic coating (85wt% Ni and 8.99wt% Ni Cr is doped with 0.01wt% Mo, 4wt% Fe and 2wt% Si, and the surface is modified by polytetrafluoroethylene-hexafluoropropylene copolymer) for tar condensation, and the front-end coupling is mainly made of quartz The reactor is used for biomass pyrolysis, and the carrier gas is N 2 , the flue gas temperature is 500°C. In actual application, the pyrolysis gas enters from the pyrolysis gas inlet 17 and flows out from the pyrolysis gas outlet 20, and the condensed working fluid enters from the condensing working fluid inlet 19 and flows out from the condensing working fluid outlet 15, completing the tar condensation work. After repeated pyrolysis, the NiCr alloy coating can reduce the tar adhesion rate...
Embodiment 3
[0041] A double-cylinder alternate tar condensation and self-cleaning device, selects heat exchange tubes 18 made of power plant steel and the outer wall of the heat exchange tubes 18 is covered with a NiCr alloy-based oleophobic coating (65wt% Ni and 18wt% Cr Doped with 4wt% Mo, 10wt% Fe and 3wt% Si, and using polytetrafluoroethylene-hexafluoropropylene copolymer for surface modification) for tar condensation, the front end is coupled to a reactor made of quartz as the main material For biomass pyrolysis, choose N as the carrier gas 2, the flue gas temperature is 500°C. In actual application, the pyrolysis gas enters from the pyrolysis gas inlet 17 and flows out from the pyrolysis gas outlet 20, and the condensed working fluid enters from the condensing working fluid inlet 19 and flows out from the condensing working fluid outlet 15, completing the tar condensation work. After multiple pyrolysis, the NiCr alloy coating can reduce the tar adhesion rate up to 60%. To clean th...
PUM
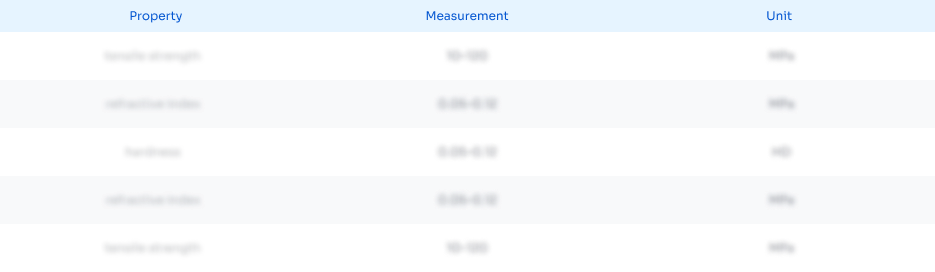
Abstract
Description
Claims
Application Information

- R&D Engineer
- R&D Manager
- IP Professional
- Industry Leading Data Capabilities
- Powerful AI technology
- Patent DNA Extraction
Browse by: Latest US Patents, China's latest patents, Technical Efficacy Thesaurus, Application Domain, Technology Topic, Popular Technical Reports.
© 2024 PatSnap. All rights reserved.Legal|Privacy policy|Modern Slavery Act Transparency Statement|Sitemap|About US| Contact US: help@patsnap.com