Aerial operation robot carrying double longitudinal active telescopic mechanical arms
A technology for working robots and mechanical arms, which is applied to manipulators, unmanned aerial vehicles, claw arms, etc., can solve the problems of changing working conditions, low working efficiency, poor safety, etc. Effect
- Summary
- Abstract
- Description
- Claims
- Application Information
AI Technical Summary
Problems solved by technology
Method used
Image
Examples
Embodiment 1
[0033] Embodiment 1: as Figure 1 to Figure 5 As shown, an aerial work robot equipped with a self-balancing mechanical arm includes a flying platform 1, a self-balancing telescopic system 2 fixedly connected to the bottom of the flying platform 1, a fixed rod 3 connected to the bottom of the flying platform 1, and a fixed rod connected to the fixed rod. 3 the rotating bracket 4 at the end, the mechanical arm 6 connected to the rotating bracket 4 through the pipe clamp 5, the operating system 8 connected to the front end of the mechanical arm 6, the power supply system 7 connected to the end of the mechanical arm for the mechanical arm 6 and the operating system 8 to work, There is a rotating shaft at both ends of the pipe clamp 5, which can rotate around the rotating bracket.
[0034] Preferably, the above-mentioned self-balancing manipulator system 2 includes a mounting plate 201 connected to the bottom of the flight platform 1, a steering gear 202 fixed on the mounting plate...
Embodiment 2
[0040] Embodiment 2: as Figure 2 to Figure 5 As shown, the control method of the self-balancing telescopic system of the flying platform 1 under different attitudes is as follows:
[0041] When the attitude of the aerial robot is horizontal, the steering gear arm 203 and the mechanical arm 6 are also in a horizontal state, as figure 2 As shown, the self-balancing controller obtains the pitch angle data of the flying platform in real time through Bluetooth, and controls the steering gear 202 to rotate the steering gear arm 203 to drive the reciprocating rod 205 to reciprocate through the PID control algorithm, so that it automatically follows the pitch angle change of the flying platform, thereby Keep the mechanical arm 6 in a horizontal state.
[0042] When the pitch angle of the aerial robot is greater than 0, the pitch angle is Y 1 , deviation E 1 =Y 1 -0; when the pitch angle is greater than 0, the pitch angle is Y 2 , deviation E 2 =0-Y 2 , the time for the attitud...
PUM
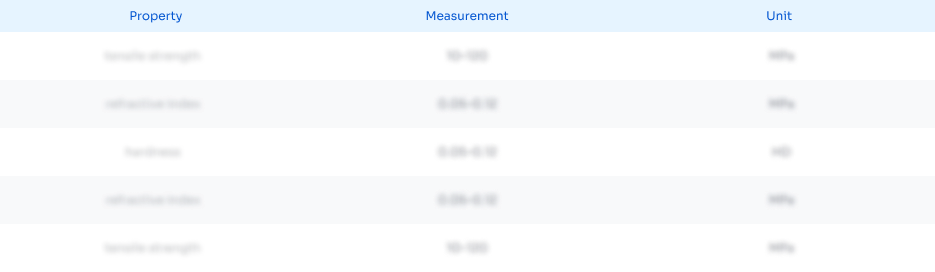
Abstract
Description
Claims
Application Information

- R&D
- Intellectual Property
- Life Sciences
- Materials
- Tech Scout
- Unparalleled Data Quality
- Higher Quality Content
- 60% Fewer Hallucinations
Browse by: Latest US Patents, China's latest patents, Technical Efficacy Thesaurus, Application Domain, Technology Topic, Popular Technical Reports.
© 2025 PatSnap. All rights reserved.Legal|Privacy policy|Modern Slavery Act Transparency Statement|Sitemap|About US| Contact US: help@patsnap.com