Method for producing polymer
A manufacturing method and polymer technology, applied in the field of polymer manufacturing, can solve the problems of increase, damage of stirring paddle, high viscosity, etc.
- Summary
- Abstract
- Description
- Claims
- Application Information
AI Technical Summary
Problems solved by technology
Method used
Image
Examples
Embodiment 1
[0194] A 200 mL reaction flask was charged with (A) 12.6 g of monoallyl diglycidyl isocyanuric acid, (B) 6.6 g of adipic acid, and (C) ethyltriphenylphosphonium bromide as a polymerization catalyst 0.84 g, (D) 0.18 g of pyridine as a co-catalyst, and 60 g of propylene glycol monomethyl ether were used to prepare a raw material solution. The molar ratio of (C)component and (D)component is 1:1, and the equivalent ratio of (A)component and (B)component is 1:1.01.
[0195] Next, this solution was heated and refluxed at 121° C., and reacted for 1 to 6 hours to synthesize a polymer. GPC analysis of the produced polymer showed that Mw=6400 at 1 hour after reaching reflux temperature, Mw=10100 at 2 hours, Mw=10500 at 4 hours, Mw=10400 at 5 hours, and at 6 hours Mw=10400, after 4 hours after reaching the reflux temperature, the weight average molecular weight Mw stabilized.
Embodiment 2
[0197] A 200 mL reaction flask was charged with (A) 12.6 g of monoallyl diglycidyl isocyanuric acid, (B) 6.6 g of adipic acid, and (C) ethyltriphenylphosphonium bromide as a polymerization catalyst 0.84 g, (D) 0.26 g of pyridine as a co-catalyst, and 60 g of propylene glycol monomethyl ether were used to prepare a raw material solution. The molar ratio of (C)component and (D)component is 1:1.5, and the equivalent ratio of (A)component and (B)component is 1:1.01.
[0198] Next, this solution was heated and refluxed at 121° C., and reacted for 1 to 7 hours to synthesize a polymer. GPC analysis of the produced polymer showed that Mw=6500 in the first hour after reaching the reflux temperature, Mw=8100 in the second hour, Mw=8100 in the fourth hour, Mw=8000 in the fifth hour, and Mw in the sixth hour Mw = 7900, Mw = 7800 at the 7th hour, and the weight average molecular weight Mw was stabilized after 2 hours after reaching the reflux temperature.
Embodiment 3
[0200] A 200 mL reaction flask was charged with (A) 12.6 g of monoallyl diglycidyl isocyanuric acid, (B) 6.6 g of adipic acid, and (C) ethyltriphenylphosphonium bromide as a polymerization catalyst 0.84 g, (D) 0.09 g of pyridine as a co-catalyst, and 60 g of propylene glycol monomethyl ether were used to prepare a raw material solution. The molar ratio of (C)component and (D)component is 1:0.5, and the equivalent ratio of (A)component and (B)component is 1:1.01.
[0201]Next, this solution was heated and refluxed at 121° C., and reacted for 1 to 7 hours to synthesize a polymer. GPC analysis of the produced polymer showed that Mw=8500 in the first hour after reaching the reflux temperature, Mw=13200 in the second hour, Mw=15000 in the fourth hour, Mw=14900 in the fifth hour, and Mw in the sixth hour Mw=14800 at 7 hours, Mw=14600 at 7 hours, after 4 hours after reaching the reflux temperature, the weight average molecular weight Mw stabilized.
PUM
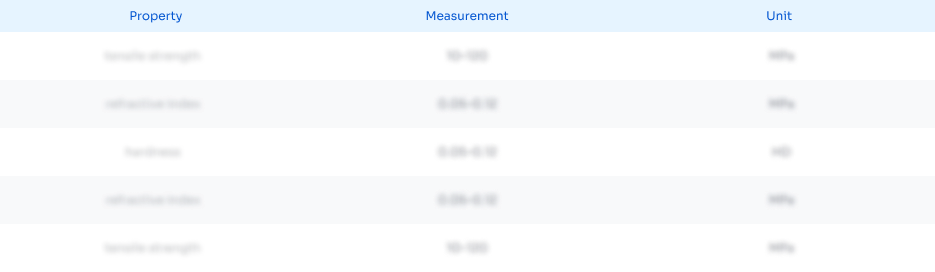
Abstract
Description
Claims
Application Information

- Generate Ideas
- Intellectual Property
- Life Sciences
- Materials
- Tech Scout
- Unparalleled Data Quality
- Higher Quality Content
- 60% Fewer Hallucinations
Browse by: Latest US Patents, China's latest patents, Technical Efficacy Thesaurus, Application Domain, Technology Topic, Popular Technical Reports.
© 2025 PatSnap. All rights reserved.Legal|Privacy policy|Modern Slavery Act Transparency Statement|Sitemap|About US| Contact US: help@patsnap.com