Asbestos cement and production process thereof
A technology of asbestos cement and production process, which is applied in the field of cement production, can solve the problems of affecting human health, high cost, affecting the mixing effect of asbestos wool, etc., and achieve the effect of protecting human health and reducing harmfulness
- Summary
- Abstract
- Description
- Claims
- Application Information
AI Technical Summary
Problems solved by technology
Method used
Examples
Embodiment Construction
[0025] The technical solutions in the embodiments of the present invention will be clearly and completely described below. Obviously, the described embodiments are only some of the embodiments of the present invention, but not all of them. Based on the embodiments of the present invention, all other embodiments obtained by persons of ordinary skill in the art without creative efforts fall within the protection scope of the present invention.
[0026] An asbestos cement, which is composed of the following raw materials in parts by weight: 30-40 parts of asbestos wool, 100-110 parts of Portland cement, 1200-1300 parts of clear water, 0.3-0.8 parts of defoaming agent, river sand bone 15-25 servings;
[0027] The specific parts by weight of each component of the asbestos cement are as follows: 30 parts of asbestos wool, 100 parts of Portland cement, 1200 parts of clear water, 0.3 parts of defoaming agent, and 15 parts of river sand aggregate;
[0028] A kind of production technol...
PUM
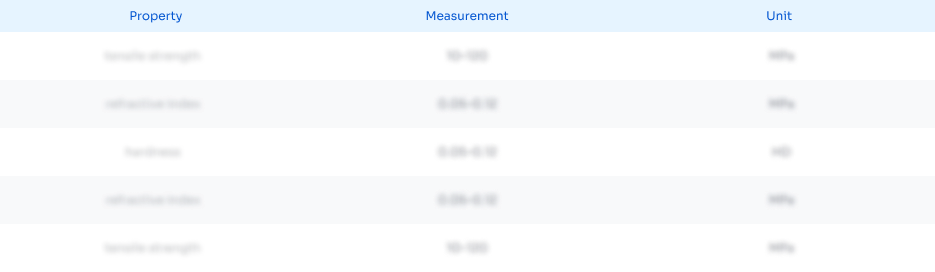
Abstract
Description
Claims
Application Information

- R&D
- Intellectual Property
- Life Sciences
- Materials
- Tech Scout
- Unparalleled Data Quality
- Higher Quality Content
- 60% Fewer Hallucinations
Browse by: Latest US Patents, China's latest patents, Technical Efficacy Thesaurus, Application Domain, Technology Topic, Popular Technical Reports.
© 2025 PatSnap. All rights reserved.Legal|Privacy policy|Modern Slavery Act Transparency Statement|Sitemap|About US| Contact US: help@patsnap.com