Acrylic emulsion pressure-sensitive adhesive and preparation method thereof
A technology of acrylic emulsion and butyl acrylate, which is applied in the direction of adhesives, adhesive types, ester copolymer adhesives, etc., can solve the problems of poor dispersion of nano-silica, high reactivity, and easy agglomeration. To achieve the effect of improving the degumming phenomenon, increasing the peel strength, and stabilizing the heat release
- Summary
- Abstract
- Description
- Claims
- Application Information
AI Technical Summary
Problems solved by technology
Method used
Image
Examples
Embodiment 1
[0027] Accurately weigh 30 grams of emulsifier nonylphenol polyoxyethylene ether ammonium sulfate (Co-436), fully dissolve in 1100 grams of deionized water, weigh 50 grams of hydroxyethyl acrylate, 80 grams of carboxyethyl acrylate, acrylic acid 3,300 grams of butyl ester and 800 grams of isobornyl acrylate were added to the aqueous solution of the emulsifier in turn under agitation to fully stir and disperse for 30 minutes to prepare a stable pre-emulsion. Add 1500 grams of water, 12 grams of buffer, and 6 grams of emulsifier NRS-10 (special alcohol ether sulfate containing allyl group, Shanghai Zhongcheng Fine Chemical Co., Ltd.) in the reaction kettle, start to heat up after stirring evenly. After the temperature was raised to 83°C, 15 grams of initiator was added to the reactor, and 50 grams of pre-emulsion was added dropwise as a seed emulsion. After the seed emulsion was added dropwise, it was kept warm for 5 minutes to allow it to fully react. After the heat preservatio...
Embodiment 2
[0029] Accurately weigh 40 grams of emulsifier nonylphenol polyoxyethylene ether ammonium sulfate, fully dissolve in 1100 grams of deionized water, weigh 50 grams of hydroxyethyl acrylate, 80 grams of carboxyethyl acrylate, and 3000 grams of butyl acrylate, 500 grams of ethyl acrylate and 500 grams of isobornyl acrylate were added to the aqueous solution of the emulsifier in turn under agitation to fully stir and disperse for 30 minutes to prepare a stable pre-emulsion. Add 1500 grams of water, 12 grams of buffer, and 6 grams of emulsifier NRS-10 into the reaction kettle, stir well and then start to heat up. After the temperature was raised to 83°C, 15 grams of initiator was added to the reactor, and 100 grams of pre-emulsion was added dropwise as the seed emulsion. After the seed emulsion was added dropwise, it was kept warm for 5 minutes to allow it to fully react. After the heat preservation is over, the remaining pre-emulsion and the aqueous solution of the initiator are a...
Embodiment 3
[0031]Accurately weigh 40 grams of emulsifier nonylphenol polyoxyethylene ether ammonium sulfate, fully dissolve in 1100 grams of deionized water, weigh 50 grams of hydroxyethyl acrylate, 50 grams of carboxyethyl acrylate, and 30 grams of methacrylic acid, 3000 grams of butyl acrylate, 600 grams of ethyl acrylate, and 600 grams of isobornyl acrylate were added to the aqueous solution of the emulsifier in turn under stirring conditions and fully stirred and dispersed for 30 minutes to form a stable pre-emulsion. Add 1500 grams of water, 12 grams of buffer, and 6 grams of emulsifier NRS-10 into the reaction kettle, stir well and then start to heat up. After the temperature was raised to 83°C, 13 grams of initiator was added to the reactor, and 0 grams of pre-emulsion was added dropwise as the seed emulsion. After the seed emulsion was added dropwise, it was kept warm for 5 minutes to allow it to fully react. After the heat preservation is over, the remaining pre-emulsion and the...
PUM
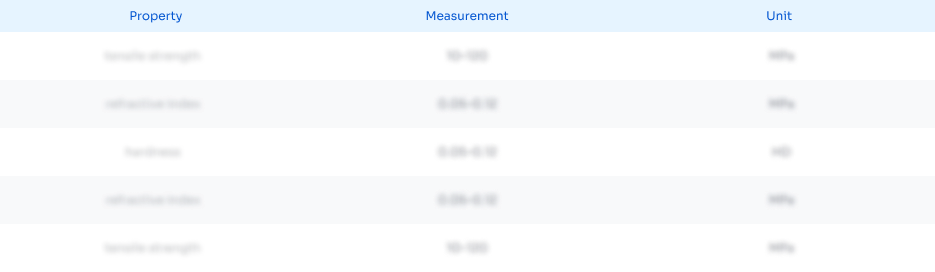
Abstract
Description
Claims
Application Information

- R&D Engineer
- R&D Manager
- IP Professional
- Industry Leading Data Capabilities
- Powerful AI technology
- Patent DNA Extraction
Browse by: Latest US Patents, China's latest patents, Technical Efficacy Thesaurus, Application Domain, Technology Topic, Popular Technical Reports.
© 2024 PatSnap. All rights reserved.Legal|Privacy policy|Modern Slavery Act Transparency Statement|Sitemap|About US| Contact US: help@patsnap.com