Manufacturing method of pressure vessel
A technology for a pressure vessel and a manufacturing method, which is applied in the field of pressure vessel manufacturing, can solve problems such as affecting the uniformity of grinding and inability to perform grinding, and achieve the effects of improving the grinding effect, improving the smoothness and improving the efficiency.
- Summary
- Abstract
- Description
- Claims
- Application Information
AI Technical Summary
Problems solved by technology
Method used
Image
Examples
Embodiment Construction
[0036] Such as Figure 1-15 Shown, a kind of pressure vessel manufacturing method comprises the following steps:
[0037] a. Cutting process: cut the metal sheet according to the specified size to obtain the sheet;
[0038] b. Bending treatment: bend the plate obtained in step a into a ring structure, cut the plate after bending, and process the wrinkles generated on the inner surface of the material to be smooth, so as to obtain the bent plate;
[0039] c. Welding treatment: place the bent plate in the welding fixture and perform welding to obtain a metal ring;
[0040] d. Grinding treatment: the metal ring is fixed on the grinding machine, and the outer wall and the inner wall are polished to obtain an annular tank body;
[0041] e, docking treatment: fix the annular tank body in step d and the pre-prepared two side end caps with tools, then weld the joint position, and then process the weld position to obtain a pressure vessel;
[0042] Wherein, described grinding machin...
PUM
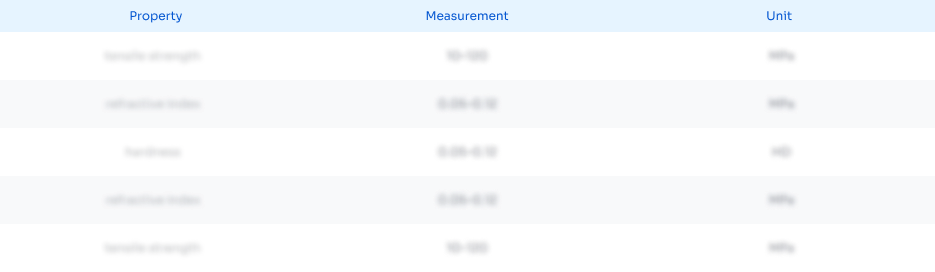
Abstract
Description
Claims
Application Information

- Generate Ideas
- Intellectual Property
- Life Sciences
- Materials
- Tech Scout
- Unparalleled Data Quality
- Higher Quality Content
- 60% Fewer Hallucinations
Browse by: Latest US Patents, China's latest patents, Technical Efficacy Thesaurus, Application Domain, Technology Topic, Popular Technical Reports.
© 2025 PatSnap. All rights reserved.Legal|Privacy policy|Modern Slavery Act Transparency Statement|Sitemap|About US| Contact US: help@patsnap.com