Feature extraction and three-dimensional reconstruction method of weld shape based on laser scanning
A technology of 3D reconstruction and feature extraction, applied in 3D modeling, image data processing, instruments, etc., can solve problems such as loss of information, difficulty in ensuring welding accuracy and efficiency, etc., to ensure efficiency, enhance visualization effects, and ensure accuracy Effect
- Summary
- Abstract
- Description
- Claims
- Application Information
AI Technical Summary
Problems solved by technology
Method used
Image
Examples
specific Embodiment approach 1
[0039] A feature extraction and three-dimensional reconstruction method of a laser scan, a three-dimensional reconstruction method of a laser scan, a three-dimensional reconstruction method according to a laser scan, characterized in that the method is first scanned according to laser scan The principle, the optical triangulation principle design optical structure system, calculates changes in weld horizontal and vertical positions by geometric relationship; wherein the entire system is mainly formed by camera and industrial control, using CCD camera to collect image acquisition, with J1900 The industrial computer is a processing unit, and the effect of image acquisition and display is given by debugging; then, the obtained raw image is used to perform a digital form filtering, denoising, etc., for pre-processed welding, by the weld identification algorithm. The seam image is identified by feature points; finally, according to the position change of the center point of the weld im...
specific Embodiment approach 2
[0041] Unlike the specific embodiment, the characteristic extraction of the weld shape based on laser scanning and three-dimensional reconstruction method, such as figure 1 As shown, the feature extraction and the three-dimensional reconstruction method include the following steps:
[0042] Step 1. After obtaining a weld image, the model is set by the visual system, and the image coordinates of the weld image in the weld image in the image coordinate system of the weld image are converted to the camera coordinate, and transformed to the coordinate based on the robotic base coordinate system. ;
[0043] Step 2, image pretreatment;
[0044] Step three, using the Harris angle detection algorithm for feature point extraction;
[0045] Step 4, using the greedy projection triangulation algorithm for triangulation, three-dimensional reconstruction process of weld images.
specific Embodiment approach 3
[0047] Different from the specific embodiment, the characteristic extraction of the weld shape based on laser scanning, the specific process of the step one, the characteristic extraction, and the three-dimensional reconstruction method.
[0048] The visual system calibration includes the calibration of the camera, the calibration of the wire structure light plane, and the hand-grade standard;
[0049]The camera is scheduled to include two parts: the calibration of the internal parametric and the calibration of the outer parameter; the calibration of the internal parametric means that the focal length of the camera, the distortion coefficient, the calibration of the central point; the calibration of the outer parametric, refers to the rotation of the camera coordinate system and the world coordinate system Relationship between matrix and mobile matrix;
[0050] There are two ways to mark the camera: traditional camera calibration and self-calibration, self-calibration does not req...
PUM
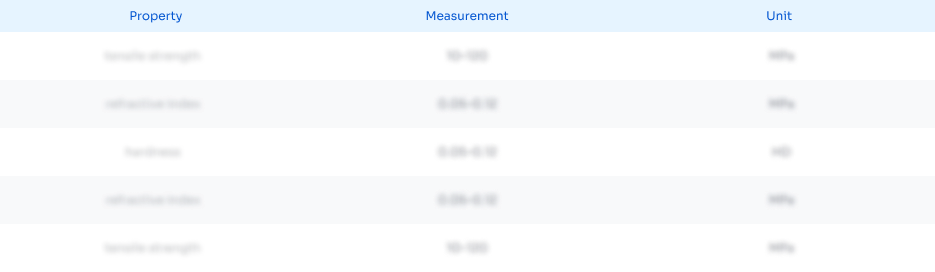
Abstract
Description
Claims
Application Information

- R&D
- Intellectual Property
- Life Sciences
- Materials
- Tech Scout
- Unparalleled Data Quality
- Higher Quality Content
- 60% Fewer Hallucinations
Browse by: Latest US Patents, China's latest patents, Technical Efficacy Thesaurus, Application Domain, Technology Topic, Popular Technical Reports.
© 2025 PatSnap. All rights reserved.Legal|Privacy policy|Modern Slavery Act Transparency Statement|Sitemap|About US| Contact US: help@patsnap.com