Automatic plate cutting, bending and welding equipment
A technology of automatic cutting and welding equipment, applied in other manufacturing equipment/tools, metal processing, manipulators, etc., can solve problems such as low grasping efficiency and lack of automated processes
- Summary
- Abstract
- Description
- Claims
- Application Information
AI Technical Summary
Problems solved by technology
Method used
Image
Examples
Embodiment Construction
[0023] Such as Figure 1-Figure 6 As shown, a plate automatic cutting, bending and welding equipment includes a plate incoming warehouse 1, a first handling manipulator 2, a laser cutting robot 4, a second handling manipulator and a bending robot 6, and two transplanting workbenches 3 are respectively set Below and on one side of the laser cutting robot 4, the first transport manipulator 2 includes a first transport manipulator body and a first transport gripper, the first transport gripper includes a gripper installation base frame 202, a suction mechanism and a gripping mechanism, The upper part of the gripper installation base frame 202 is fixedly connected with the lower part of the gripper connecting rod 201, and the upper part of the gripper connecting rod 201 is fixed on the end flange of the first handling manipulator body, and the suction mechanism is installed on the lower part of the gripper installation base frame 202, and the gripper The picking mechanism is arran...
PUM
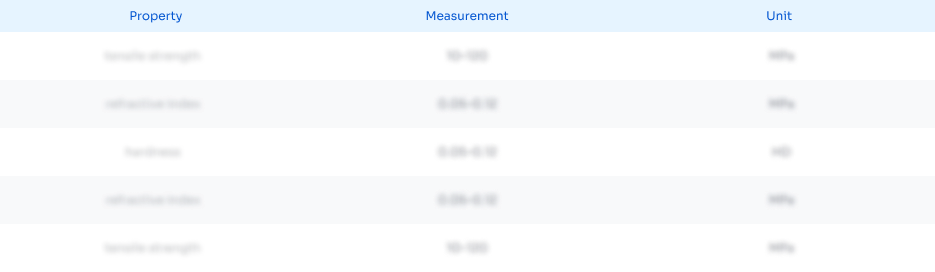
Abstract
Description
Claims
Application Information

- R&D
- Intellectual Property
- Life Sciences
- Materials
- Tech Scout
- Unparalleled Data Quality
- Higher Quality Content
- 60% Fewer Hallucinations
Browse by: Latest US Patents, China's latest patents, Technical Efficacy Thesaurus, Application Domain, Technology Topic, Popular Technical Reports.
© 2025 PatSnap. All rights reserved.Legal|Privacy policy|Modern Slavery Act Transparency Statement|Sitemap|About US| Contact US: help@patsnap.com