Method for improving welding efficiency of backfill type friction stir spot welding
A friction stir, spot welding technology, applied in welding equipment, non-electric welding equipment, metal processing equipment, etc., can solve problems such as unfavorable industrial production, long welding time, and low welding efficiency.
- Summary
- Abstract
- Description
- Claims
- Application Information
AI Technical Summary
Problems solved by technology
Method used
Image
Examples
Embodiment 1
[0029] The present invention provides a new method for improving the welding efficiency of backfill friction stir spot welding. The backfill friction stir spot welding tool is used to weld two aluminum alloy plates. The welding material used in this embodiment is 0.9mm thick 6022 -T4 aluminum alloy (upper plate) and 2.0mm thick 7075-T6 aluminum alloy (lower plate), the sample size of the upper and lower plates is 100mm×25mm; the spot welding tool consists of three parts: a compression ring, a sleeve and a stirring needle. Its diameter is 15mm, 9mm and 6mm respectively, the method is as follows figure 1 shown, including the following steps:
[0030] Before welding, use acetone to remove oil and other impurities on the surface of the workpiece. Such as figure 2 As shown, a sleeve with a threaded outer wall and a grooved bottom is used. Under the condition that the pressing and withdrawing time of the welding stirring head remains unchanged, the welding efficiency is improved...
PUM
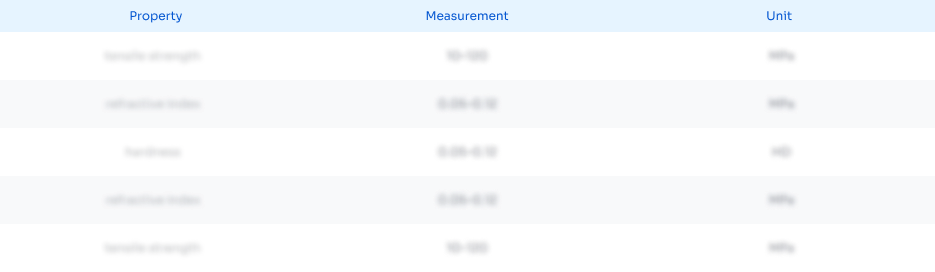
Abstract
Description
Claims
Application Information

- R&D
- Intellectual Property
- Life Sciences
- Materials
- Tech Scout
- Unparalleled Data Quality
- Higher Quality Content
- 60% Fewer Hallucinations
Browse by: Latest US Patents, China's latest patents, Technical Efficacy Thesaurus, Application Domain, Technology Topic, Popular Technical Reports.
© 2025 PatSnap. All rights reserved.Legal|Privacy policy|Modern Slavery Act Transparency Statement|Sitemap|About US| Contact US: help@patsnap.com