Automatic hot pressing equipment
A hot-pressing equipment and automatic technology, applied in the field of hot-pressing, can solve the problems of wasting heat energy and time, poor precision of hot-pressing, excessive heat, etc., and achieve the effect of saving heat energy, saving heating time, and improving hot-pressing efficiency
- Summary
- Abstract
- Description
- Claims
- Application Information
AI Technical Summary
Problems solved by technology
Method used
Image
Examples
Embodiment Construction
[0029] Next, the technical solutions in the embodiments of the present invention will be apparent from the embodiment of the present invention, and it is clearly described, and it is understood that the described embodiments are merely embodiments of the present invention, not all of the embodiments. Based on the embodiments of the present invention, there are all other embodiments obtained without making creative labor without making creative labor premises.
[0030] See Figure 1-7 The present invention provides a technical solution:
[0031]An automatic hot pressing device including housings 1, the bottom plate 2, the positioning plate 3, the silo 4, the airwand passage 5, the controller 6, and the introduction passage 7, and the housing 1 is disposed on the bottom plate 2, the housing 1 inside the bottom Set the positioning plate 3, the falling passage 5, and the controller 6, the positioning plate 3 is located at the bottom of the housing 1, and the silo 4 is disposed at the t...
PUM
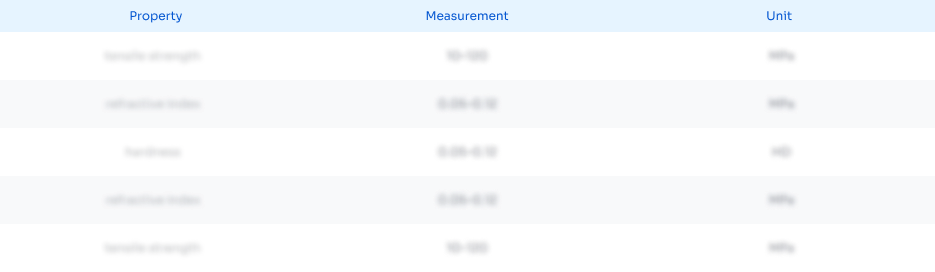
Abstract
Description
Claims
Application Information

- R&D
- Intellectual Property
- Life Sciences
- Materials
- Tech Scout
- Unparalleled Data Quality
- Higher Quality Content
- 60% Fewer Hallucinations
Browse by: Latest US Patents, China's latest patents, Technical Efficacy Thesaurus, Application Domain, Technology Topic, Popular Technical Reports.
© 2025 PatSnap. All rights reserved.Legal|Privacy policy|Modern Slavery Act Transparency Statement|Sitemap|About US| Contact US: help@patsnap.com