Speed and current double-closed-loop fuzzy control-based PMSM sensorless control method
A speed controller and fuzzy control technology, applied in the direction of motor control, motor generator control, control of electromechanical brakes, etc., can solve the problem that the PI controller cannot guarantee dynamic performance, etc. Interference ability, effect of improving sensorless control performance
- Summary
- Abstract
- Description
- Claims
- Application Information
AI Technical Summary
Problems solved by technology
Method used
Image
Examples
Embodiment Construction
[0058] The present invention will be further described below in conjunction with the accompanying drawings and embodiments.
[0059] Such as figure 1 As shown, a PMSM sensorless control method of speed and current double closed-loop fuzzy control, including the following steps:
[0060] 1) Establish the vector control mathematical model of the surface-mounted permanent magnet synchronous motor. The mathematical model of the surface-mounted permanent magnet synchronous motor based on the rotating coordinate system is as follows:
[0061]
[0062] Among them, R s is the stator resistance, u d , u q Respectively d, q axis stator voltage, i d i q Respectively d, q axis stator current, L d , L q Respectively d, q axis stator inductance, ω e is the electromagnetic speed, is the permanent magnet flux linkage.
[0063] 2) Establish fuzzy speed controller and fuzzy current controller to improve traditional PI controller based on double closed loop. Step 2) specifically ...
PUM
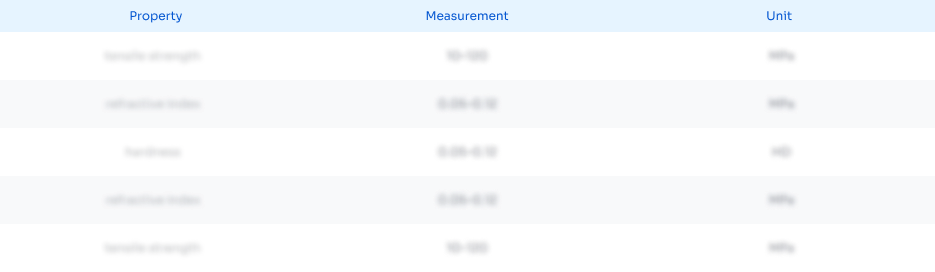
Abstract
Description
Claims
Application Information

- Generate Ideas
- Intellectual Property
- Life Sciences
- Materials
- Tech Scout
- Unparalleled Data Quality
- Higher Quality Content
- 60% Fewer Hallucinations
Browse by: Latest US Patents, China's latest patents, Technical Efficacy Thesaurus, Application Domain, Technology Topic, Popular Technical Reports.
© 2025 PatSnap. All rights reserved.Legal|Privacy policy|Modern Slavery Act Transparency Statement|Sitemap|About US| Contact US: help@patsnap.com