Die-casting machine charging barrel and injection rod
A technology for injection rods and die-casting machines, which is applied in the field of die-casting machine parts, and can solve problems such as long machine standby time, high replacement frequency of injection punches, and high cost of die-casting consumables
- Summary
- Abstract
- Description
- Claims
- Application Information
AI Technical Summary
Problems solved by technology
Method used
Image
Examples
Embodiment
[0025] Example: refer to figure 1 Shown: a die-casting machine barrel and injection rod, including a barrel 1, a number of hydraulic cylinders 2 are uniformly arranged on the front end of the arc surface of the barrel 1, and the hydraulic cylinders 2 and the barrel 1 are connected together by bolts. And the output end of the hydraulic cylinder 2 is provided with a pressure head 3, the pressure head 3 and the output end of the hydraulic cylinder 2 are connected together by bolts, the front end of the barrel 1 is provided with a plunger 4, and the plunger 4 is aligned with the front end of the barrel 1. One end is provided with injection punch 5; barrel 1 is convenient to support the raw material for die-casting, and then it is convenient to carry out die-casting treatment on the raw material; The degree of calibration is corrected, so that the injection punch 5 can be stably used in conjunction with the barrel 1, and the indenter 3 is convenient to be stuck on the arc surface o...
PUM
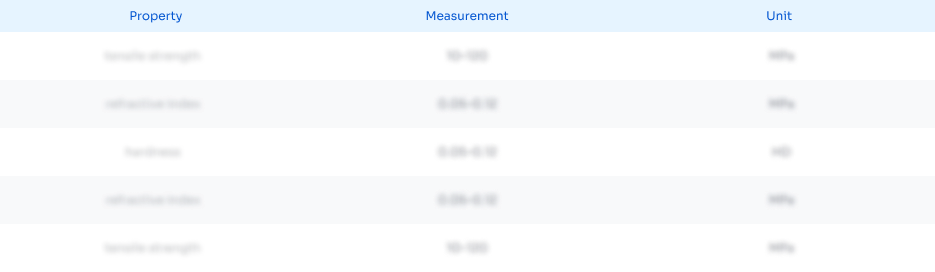
Abstract
Description
Claims
Application Information

- R&D Engineer
- R&D Manager
- IP Professional
- Industry Leading Data Capabilities
- Powerful AI technology
- Patent DNA Extraction
Browse by: Latest US Patents, China's latest patents, Technical Efficacy Thesaurus, Application Domain, Technology Topic, Popular Technical Reports.
© 2024 PatSnap. All rights reserved.Legal|Privacy policy|Modern Slavery Act Transparency Statement|Sitemap|About US| Contact US: help@patsnap.com