Machining method for grinding high-strength aeronautical part through numerical control machining center
A technology for aerospace parts and machining centers, which is applied in the direction of grinding workpiece supports, grinding machine parts, grinding drive devices, etc. Inexpensive, low runout, short shank length effects
- Summary
- Abstract
- Description
- Claims
- Application Information
AI Technical Summary
Problems solved by technology
Method used
Image
Examples
Embodiment 1
[0044] like Figure 4 to Figure 6 As shown in the figure, the machining method of grinding high-strength aerospace parts by CNC machining center includes the following steps:
[0045] S1. Clamping: Clamp the product 5 on the worktable 3, clamp one end of the tool bar 1 on the machine tool spindle 4, and clamp the grinding wheel 2 at the other end;
[0046] S2. The grinding wheel 2 is rotated through the rotation of the machine tool spindle 4, the speed S is 8000~10000r / min, and the XY axis of the machine tool is linked to feed, the feed rate F is 100~120mm / min, and the grinding surface is the two sides of a certain type of landing gear. There are two parallel planes, the movement track of grinding wheel 2 is parallel to the grinding surface, adjust the knife compensation value, according to the difference between the actual value and the required value, and then select the appropriate number of knife compensation values, and control each knife compensation within 0.05mm, Diff...
Embodiment 2
[0052] like Figure 7 to Figure 9 As shown in the figure, the machining method of grinding high-strength aerospace parts by CNC machining center includes the following steps:
[0053] S1. Clamping: Clamp the product 5 on the worktable 3, clamp one end of the tool bar 1 on the machine tool spindle 4, and clamp the grinding wheel 2 at the other end;
[0054] S2. The grinding wheel 2 is rotated by the rotation of the machine tool spindle 4, the speed S is 8000~10000r / min, and the XY axis of the machine tool is linked to feed, the feed rate F is 100~120mm / min, and the grinding surface is a certain type of landing gear. Cylindrical surface, the movement trajectory of grinding wheel 2 is parallel to the grinding surface, that is, the movement trajectory of grinding wheel 2 is circular, adjust the tool compensation value so that the cylinder of the part is guaranteed to be ∅60 (-0.10 / -0.126) mm, ∅60.5 (-0.10 / -0.126) mm, preferably, the parameter is F=100mm / min.
[0055] Further, i...
PUM
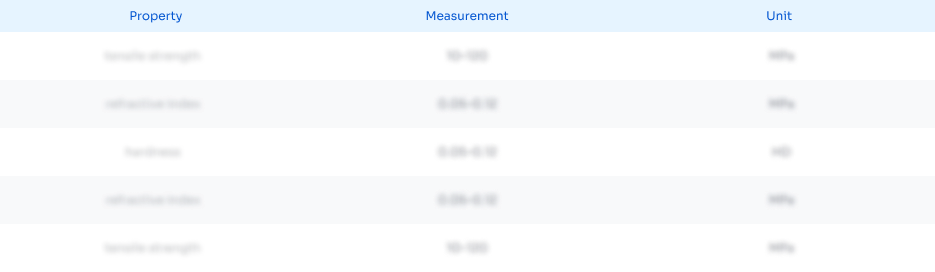
Abstract
Description
Claims
Application Information

- R&D Engineer
- R&D Manager
- IP Professional
- Industry Leading Data Capabilities
- Powerful AI technology
- Patent DNA Extraction
Browse by: Latest US Patents, China's latest patents, Technical Efficacy Thesaurus, Application Domain, Technology Topic, Popular Technical Reports.
© 2024 PatSnap. All rights reserved.Legal|Privacy policy|Modern Slavery Act Transparency Statement|Sitemap|About US| Contact US: help@patsnap.com