Heat treatment technology of thin-wall bearing ring
A technology of thin-walled bearings and rings, which is applied in the field of bearing processing, can solve the problems of product deformation size that cannot meet the technical requirements, outer diameter deformation, etc., and achieve the effect of reducing residual stress and grinding stress
- Summary
- Abstract
- Description
- Claims
- Application Information
AI Technical Summary
Problems solved by technology
Method used
Image
Examples
Embodiment Construction
[0007] The present invention will be further described below in conjunction with specific examples.
[0008] The heat treatment process for a thin-walled bearing ring includes:
[0009] 1. Stress relief annealing for forging and turning: the annealing temperature is 620-660°C, and the holding time is 6-8 hours.
[0010] 2. Heat treatment and tempering process: the first tempering temperature is 160-180°C, the holding time is 3-4h; the second tempering temperature is 190-210°C, and the holding time is 3-4h.
[0011] 3. Additional tempering process for removal of grinding: the first additional tempering temperature is 140-160°C, holding time 3-4h; the second additional tempering temperature is 140-160°C, holding time: 3-4h.
[0012] According to the above technical scheme, 50 pieces of thin-walled bearing rings were processed, and the test data showed that the deformation of the bearing rings after final grinding met the technical requirements.
PUM
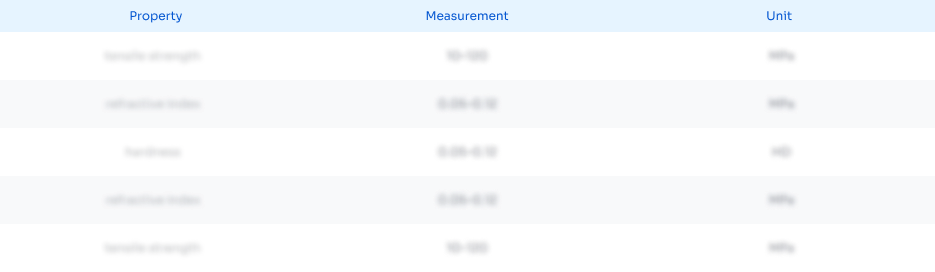
Abstract
Description
Claims
Application Information

- R&D
- Intellectual Property
- Life Sciences
- Materials
- Tech Scout
- Unparalleled Data Quality
- Higher Quality Content
- 60% Fewer Hallucinations
Browse by: Latest US Patents, China's latest patents, Technical Efficacy Thesaurus, Application Domain, Technology Topic, Popular Technical Reports.
© 2025 PatSnap. All rights reserved.Legal|Privacy policy|Modern Slavery Act Transparency Statement|Sitemap|About US| Contact US: help@patsnap.com