Welding forming machine as well as production line and production method of cement floor support plate
A production method and technology of floor decks, applied in the field of cement floor decks, can solve problems such as reduced production efficiency, large and clumsy cost of process equipment, and impact on production costs, so as to reduce production and equipment costs, and achieve stable and reliable welding and connection. reliable performance
- Summary
- Abstract
- Description
- Claims
- Application Information
AI Technical Summary
Problems solved by technology
Method used
Image
Examples
Embodiment 1
[0047] Such as Figure 1-4 As shown, this embodiment proposes a welding forming machine, including a positive electrode 1 and a negative electrode 2 both arranged on the upper part of the workpiece. sides.
[0048] Such as figure 1 As shown, it also includes a positive electrode copper column 3, the bottom of which is connected to the positive electrode 1; one side of the positive electrode copper column 3 is provided with a negative electrode copper column 4, and the negative electrode copper column 4 is connected to the negative electrode 2, and the negative electrode copper column 4 is also sleeved There are springs 5. Wherein the bottom end of spring 5 is fixedly connected with negative electrode 2 and / or negative electrode copper column 4, and the upper end of spring 5 is fixedly connected with fixed block, and this fixed block is fixedly connected with the main body of welding molding machine, thereby makes under the effect of spring 5, The negative electrode 2 drives...
Embodiment 2
[0060] Such as Figure 5-10 As shown, this embodiment proposes a cement floor deck production line, including intelligent assembly equipment for steel mesh and steel truss;
[0061] Automatic welding forming machine for steel mesh and steel truss used to weld steel mesh and steel truss to form steel skeleton;
[0062] Intelligent assembly equipment for cement floor slabs used for steel skeleton and floor slab bottom formwork assembly;
[0063] Automatic welding and forming equipment for cement floor deck. The automatic welding and forming equipment for cement floor deck includes an intelligent conveyor and a welding forming machine described in Embodiment 1. The welding forming machine is used for welding the steel skeleton and the bottom mold of the floor deck;
[0064] Components are automatically transported on the transit track and finished components are automatically off-line and put into storage.
[0065] Through technological innovation and multi-group equipment coll...
PUM
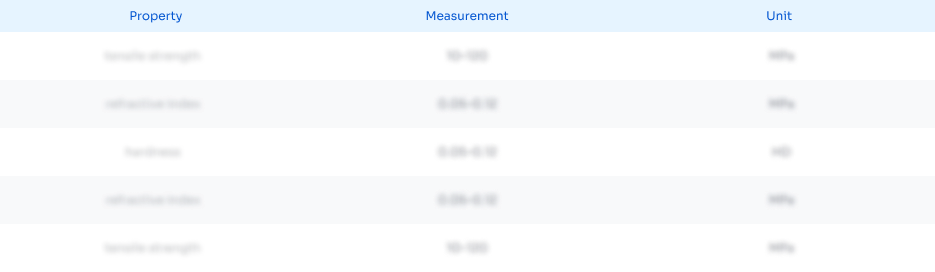
Abstract
Description
Claims
Application Information

- R&D
- Intellectual Property
- Life Sciences
- Materials
- Tech Scout
- Unparalleled Data Quality
- Higher Quality Content
- 60% Fewer Hallucinations
Browse by: Latest US Patents, China's latest patents, Technical Efficacy Thesaurus, Application Domain, Technology Topic, Popular Technical Reports.
© 2025 PatSnap. All rights reserved.Legal|Privacy policy|Modern Slavery Act Transparency Statement|Sitemap|About US| Contact US: help@patsnap.com