A self-adaptive flexible low-stress clamping device and clamping method for deep-sag aspheric elements
A technology of Fukaya Takafi and clamping device, which is applied in the direction of workpiece clamping device and manufacturing tools, which can solve the problems of low clamping precision and inability to fully fit, so as to improve clamping precision and processing precision, and facilitate clamping , to avoid the effect of local stress concentration
- Summary
- Abstract
- Description
- Claims
- Application Information
AI Technical Summary
Problems solved by technology
Method used
Image
Examples
Embodiment Construction
[0043] The technical solutions in the embodiments of the present invention will be clearly and completely described below in conjunction with the accompanying drawings. Obviously, the described embodiments are only some of the embodiments of the present invention, not all of them. Based on the embodiments of the present invention, all other embodiments obtained by persons of ordinary skill in the art without making creative efforts belong to the protection scope of the present invention.
[0044] Such as Figure 1-2 As shown, the present invention provides an adaptive flexible low-stress clamping device for deep sagittal aspheric elements, including a vacuum adsorption base 1, a number of flexible support units 2, a dual-channel rotary joint 3, an air pipe 4, a top ring 6, a sealing circle 7, self-centering chuck 8 and high-precision CNC rotary table 9; among them,
[0045] The vacuum adsorption base 1 is fixed on the high-precision numerical control rotary table 9 through th...
PUM
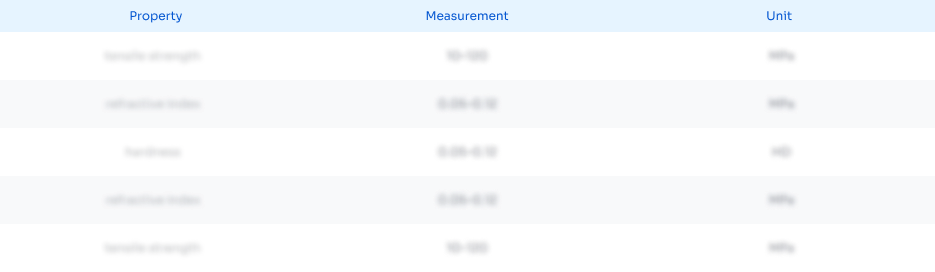
Abstract
Description
Claims
Application Information

- R&D
- Intellectual Property
- Life Sciences
- Materials
- Tech Scout
- Unparalleled Data Quality
- Higher Quality Content
- 60% Fewer Hallucinations
Browse by: Latest US Patents, China's latest patents, Technical Efficacy Thesaurus, Application Domain, Technology Topic, Popular Technical Reports.
© 2025 PatSnap. All rights reserved.Legal|Privacy policy|Modern Slavery Act Transparency Statement|Sitemap|About US| Contact US: help@patsnap.com