Production and manufacturing method of copper bar body
A manufacturing method and rod body technology, which is applied in the field of insulating rigid cable components, socket connectors, and copper bar rods, can solve the problem of high structural strength of copper bar cable components, difficulty in controlling internal space, and difficulty in achieving structural strength and insulation performance Higher requirements and other issues, to achieve the effect of improving insulation performance and copper bar bonding strength and environmental reliability, reducing processing defect rate and process difficulty, improving structural characteristics and processing feasibility
- Summary
- Abstract
- Description
- Claims
- Application Information
AI Technical Summary
Problems solved by technology
Method used
Image
Examples
Embodiment Construction
[0035] Further detailed description will be made below in conjunction with the accompanying drawings and preferred embodiments.
[0036] An embodiment of a manufacturing method for a copper row bar body, combining Figure 1 to Figure 7 , including the following steps:
[0037] According to the specifications of the final forming of the copper bar body, a plurality of copper bars 1 are stamped in batches, and the front and rear ends of each copper bar are respectively bent so that the front end of the copper bar has a front contact 11, and the rear end of the copper bar has a rear contact. The end contact piece 12, the front / rear end contact piece is perpendicular to the plane where the copper bar is located, and then the copper bar is deburred to make the surface of the copper bar smooth; then the deburred copper bar is subjected to overall electroplating treatment to improve the oxidation resistance .
[0038] Prepare a plurality of insulating boards. In this embodiment, th...
PUM
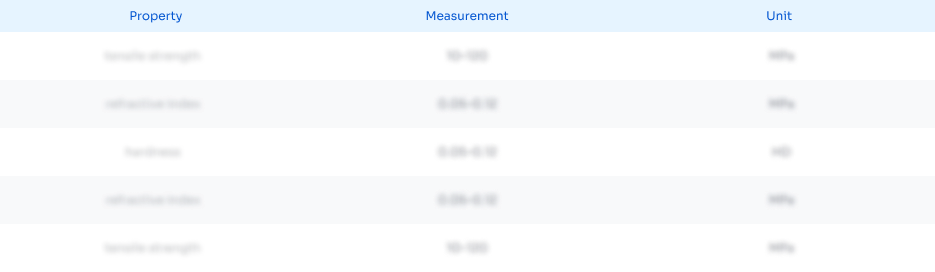
Abstract
Description
Claims
Application Information

- R&D
- Intellectual Property
- Life Sciences
- Materials
- Tech Scout
- Unparalleled Data Quality
- Higher Quality Content
- 60% Fewer Hallucinations
Browse by: Latest US Patents, China's latest patents, Technical Efficacy Thesaurus, Application Domain, Technology Topic, Popular Technical Reports.
© 2025 PatSnap. All rights reserved.Legal|Privacy policy|Modern Slavery Act Transparency Statement|Sitemap|About US| Contact US: help@patsnap.com