Fluid-solid interaction mechanical metamaterial pipeline structure for vibration attenuation and noise elimination and manufacturing method thereof
A fluid-structure coupling, metamaterial technology, applied in the direction of pipe components, mechanical equipment, pipes/pipe joints/pipe fittings, etc., can solve the problem of difficult to achieve low-frequency broadband vibration reduction and noise reduction, and achieve good low-frequency effects.
- Summary
- Abstract
- Description
- Claims
- Application Information
AI Technical Summary
Problems solved by technology
Method used
Image
Examples
Embodiment Construction
[0037] The present invention is based on the innovative design method of mechanical super material, introduces the design idea of the structural low frequency broadband to the pipeline design, overcoming the shortcomings of the traditional noise reduction measures of the pipeline. Mechanical super material refers to a "new material" that can achieve extraordinary physical properties in the subpoope long band in the cycle or non-cycle of continuous media, which can achieve "new materials" that is quite different from substances in nature in the subpoope long band, which can achieve elastic waves and acoustic waves. Emperous manipulation makes it in many areas of application prospects, such as stealth cloaks, lenses, acoustic imaging, sound sieves, vibration and noise reduction.
[0038] In order to make the objectives, technical solutions and advantages of the present invention, the present invention will be described in further detail below with reference to the accompanying dra...
PUM
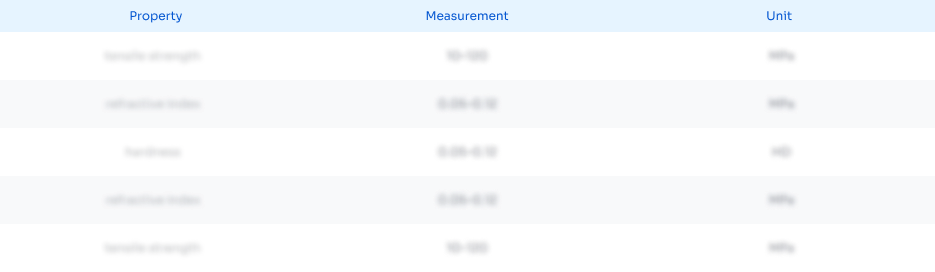
Abstract
Description
Claims
Application Information

- R&D
- Intellectual Property
- Life Sciences
- Materials
- Tech Scout
- Unparalleled Data Quality
- Higher Quality Content
- 60% Fewer Hallucinations
Browse by: Latest US Patents, China's latest patents, Technical Efficacy Thesaurus, Application Domain, Technology Topic, Popular Technical Reports.
© 2025 PatSnap. All rights reserved.Legal|Privacy policy|Modern Slavery Act Transparency Statement|Sitemap|About US| Contact US: help@patsnap.com