Method for synchronously separating potassium, lead and iron in sintering machine head ash
A technology of synchronous separation and head ash, applied in the chemical industry, can solve the problems of irritating odor of sodium sulfide, long flotation process, complex process, etc., to reduce leaching and filtration processes, increase product value, and good separation effect Effect
- Summary
- Abstract
- Description
- Claims
- Application Information
AI Technical Summary
Problems solved by technology
Method used
Image
Examples
Embodiment 1
[0047] Synchronously separate potassium, lead and iron in the sintering head ash with the following method steps:
[0048] a. Prepare pulp: mix the sintering head ash (kg) and water (L) in Table 1 according to the solid-to-liquid ratio of 1:6 to prepare pulp;
[0049] b. Slurry re-election: use a pump to transport it to the FX150 cyclone for single-stage cyclone classification. The feeding pressure of the slurry is 0.16MPa, and the diameter of the grit nozzle of the cyclone is 22mm to obtain lead-containing material Ore slurry and iron-containing slurry;
[0050] c. Separating iron and lead: filtering the obtained lead-containing material ore slurry and iron-containing material ore slurry respectively in step b to obtain lead-containing material and filtrate thereof, iron-containing material and filtrate thereof;
[0051] d. Separation of potassium: mix the filtrate obtained after filtering in step c, return to step a instead of water for pulping, and cycle through pulping-gr...
Embodiment 2
[0054] Synchronously separate potassium, lead and iron in the sintering head ash with the following method steps:
[0055] a. Prepare pulp: mix the sintering head ash (kg) and water (L) in Table 1 according to the solid-to-liquid ratio of 1:8 to prepare pulp;
[0056] b. Slurry re-election: transport it to the FX100 cyclone with a pump for primary cyclone classification, the feeding pressure of the slurry is 0.11MPa, the diameter of the grit nozzle of the cyclone is 14mm, and the gravity separation slurry is obtained , layered to obtain the primary gravity separation light phase slurry and the primary gravity separation heavy phase slurry; the primary gravity separation heavy phase slurry and water are adjusted to a solid-liquid ratio of 1:15 to make a slurry, which is transported to the The secondary cyclone classification is carried out in the FX175 cyclone, the feeding pressure of the slurry conveying is 0.15~0.18MPa, the diameter of the grit nozzle of the cyclone is 32mm, ...
Embodiment 3
[0061] Synchronously separate potassium, lead and iron in the sintering head ash with the following method steps:
[0062] a. Preparation of pulp: mix the sintering head ash (kg) and water (L) in Table 1 according to the solid-to-liquid ratio of 1:3, and prepare the pulp;
[0063] b. Slurry re-election: use a pump to transport it to the FX175 cyclone for single-stage cyclone classification. The feeding pressure of the slurry is 0.2MPa, and the diameter of the grit nozzle of the cyclone is 18mm. Select the light phase slurry and the first-stage gravity-selected heavy-phase slurry; the first-stage gravity-selected heavy-phase slurry is swirled and classified again under the same conditions as above to obtain the second-stage gravity-selected light-phase slurry and the second-stage gravity-selected heavy phase slurry;
[0064] c. Separation of iron and lead: mix the first-level gravity separation light-phase slurry obtained in step b with the second-level gravity separation ligh...
PUM
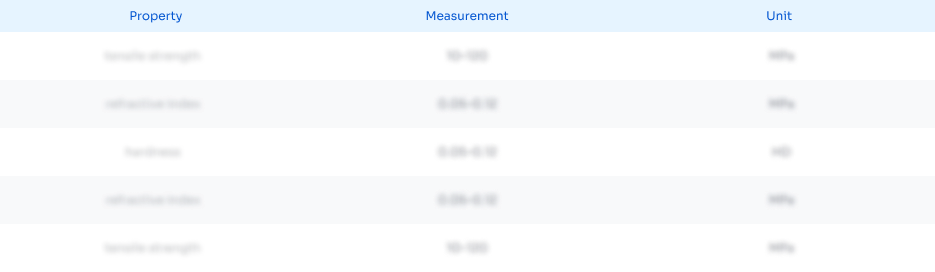
Abstract
Description
Claims
Application Information

- R&D Engineer
- R&D Manager
- IP Professional
- Industry Leading Data Capabilities
- Powerful AI technology
- Patent DNA Extraction
Browse by: Latest US Patents, China's latest patents, Technical Efficacy Thesaurus, Application Domain, Technology Topic, Popular Technical Reports.
© 2024 PatSnap. All rights reserved.Legal|Privacy policy|Modern Slavery Act Transparency Statement|Sitemap|About US| Contact US: help@patsnap.com