A frame for driverless wire-controlled chassis
An unmanned, wire-controlled technology, applied to vehicle components, substructure, transportation and packaging, etc., can solve the problems of reduced ability to withstand alternating loads, large local stress at the plate weld, limited length of the fixed screw, etc. , to achieve the effect of improving the ability to withstand alternating loads, improving the overall reliability, and increasing the length of force
- Summary
- Abstract
- Description
- Claims
- Application Information
AI Technical Summary
Problems solved by technology
Method used
Image
Examples
Embodiment Construction
[0021] The technical solutions in the embodiments of the present invention will be clearly and completely described below with reference to the accompanying drawings in the embodiments of the present invention. Obviously, the described embodiments are only a part of the embodiments of the present invention, but not all of the embodiments.
[0022] like Figure 1-5 As shown, a frame for an unmanned drive-by-wire chassis includes a carriage mounting surface 1, a wire-controlled brake system mounting bracket 2, a rear anti-collision buffer mechanism mounting surface 3, and a front anti-collision buffer mechanism mounting surface 6. Suspension mounting bracket group 4 and front suspension mounting bracket group 7, battery mounting box 5, electrical device mounting box 8.
[0023] Preferably, the brake-by-wire system mounting bracket 2 is composed of a connection block 9 and a bolt-fixed bushing 10 ; the number of the connection block 9 includes but is not limited to one piece, and...
PUM
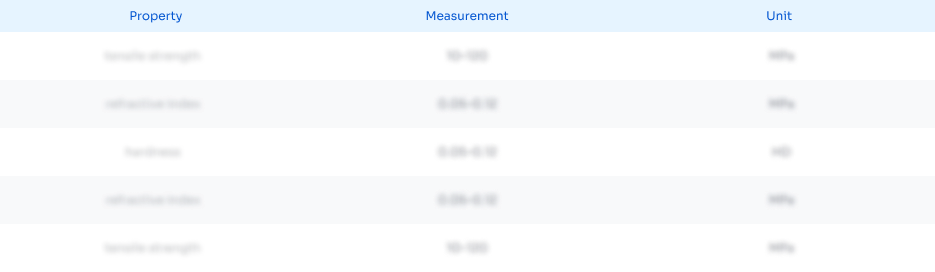
Abstract
Description
Claims
Application Information

- Generate Ideas
- Intellectual Property
- Life Sciences
- Materials
- Tech Scout
- Unparalleled Data Quality
- Higher Quality Content
- 60% Fewer Hallucinations
Browse by: Latest US Patents, China's latest patents, Technical Efficacy Thesaurus, Application Domain, Technology Topic, Popular Technical Reports.
© 2025 PatSnap. All rights reserved.Legal|Privacy policy|Modern Slavery Act Transparency Statement|Sitemap|About US| Contact US: help@patsnap.com