Welding process for manufacturing boiler economizer
A welding process and economizer technology, used in manufacturing tools, welding equipment, auxiliary welding equipment, etc., can solve the problems of low welding efficiency, inability to batch welding, failure, etc., to enhance the welding effect and realize batch welding. Effect
- Summary
- Abstract
- Description
- Claims
- Application Information
AI Technical Summary
Problems solved by technology
Method used
Image
Examples
Embodiment Construction
[0035] In order to make it easy to understand the technical means, creation features, achieved goals and effects of the present invention, the present invention will be further described below with reference to the specific figures. It should be noted that the embodiments in the present application and the features of the embodiments may be combined with each other in the case of no conflict.
[0036] like Figure 1 to Figure 9 As shown, a boiler economizer manufacturing welding process, the boiler economizer manufacturing welding process adopts the following equipment for welding, the equipment includes a base 1, a fixing device 2 and a welding device 3, the lower end of the base 1 and the The existing ground is connected, a fixing device 2 is installed on the upper end of the base 1 , and a welding device 3 is arranged above the fixing device 2 .
[0037] The fixing device 2 includes a support plate 20, a support table 21, a fixed plate 22, a horizontal plate 23, an I-shape...
PUM
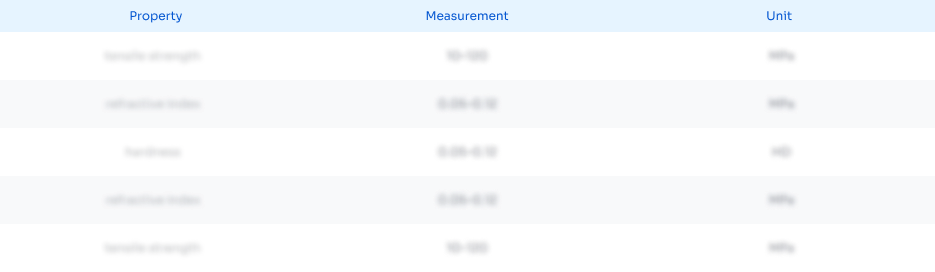
Abstract
Description
Claims
Application Information

- R&D Engineer
- R&D Manager
- IP Professional
- Industry Leading Data Capabilities
- Powerful AI technology
- Patent DNA Extraction
Browse by: Latest US Patents, China's latest patents, Technical Efficacy Thesaurus, Application Domain, Technology Topic, Popular Technical Reports.
© 2024 PatSnap. All rights reserved.Legal|Privacy policy|Modern Slavery Act Transparency Statement|Sitemap|About US| Contact US: help@patsnap.com