Heat treatment process for improving oxygen reduction catalytic activity of non-noble metal catalyst
A catalytically active, non-precious metal technology, used in electrical components, battery electrodes, circuits, etc., can solve the problems of high load and high cost
- Summary
- Abstract
- Description
- Claims
- Application Information
AI Technical Summary
Problems solved by technology
Method used
Image
Examples
Embodiment 1
[0036] Dissolve 0.3232g of ferric nitrate nonahydrate and 2.7369g of zinc nitrate hexahydrate in 400ml of methanol solution, and stir on a magnetic stirrer until the prepolymer solid is completely dissolved. Then, 4.105 g of 2-methylimidazole was added into 400 ml of methanol solution, and stirred on a magnetic stirrer until the 2-methylimidazole was completely dissolved. Next, the above two mixture solutions were poured into a three-necked flask, and heated in a water bath at 60° C. for 24 h. The supernatant of the reacted sample was poured off, the sample was centrifuged, washed, and vacuum-dried at 60° C. for 12 hours. The above-mentioned dried samples were heated up to 200° C. at a rate of 5° C. / min under an Ar atmosphere, and kept at this temperature for 1 h. Then, the temperature was raised from 200°C to 1000°C at the same rate of 5°C / min, and the calcination was maintained for 1 h. Cool naturally to obtain a Fe-N-C catalyst sample.
Embodiment 2
[0038] Dissolve 0.3232g of ferric nitrate nonahydrate and 2.7369g of zinc nitrate hexahydrate in 400ml of methanol solution, and stir on a magnetic stirrer until the prepolymer solid is completely dissolved. Then, 4.105 g of 2-methylimidazole was added into 400 ml of methanol solution, and stirred on a magnetic stirrer until the 2-methylimidazole was completely dissolved. Next, the above two mixture solutions were poured into a three-necked flask, and heated in a water bath at 60° C. for 24 h. The supernatant of the reacted sample was poured off, the sample was centrifuged, washed, and vacuum-dried at 60° C. for 12 hours. The above-mentioned dried samples were heated up to 300° C. at a rate of 5° C. / min under an Ar atmosphere, and kept at this temperature for 1 h. Then, the temperature was raised from 300°C to 1000°C at the same rate of 5°C / min, and the calcination was maintained for 1 h. Cool naturally to obtain a Fe-N-C catalyst sample.
Embodiment 3
[0040]Dissolve 0.3232g of ferric nitrate nonahydrate and 2.7369g of zinc nitrate hexahydrate in 400ml of methanol solution, and stir on a magnetic stirrer until the prepolymer solid is completely dissolved. Then, 4.105 g of 2-methylimidazole was added into 400 ml of methanol solution, and stirred on a magnetic stirrer until the 2-methylimidazole was completely dissolved. Next, the above two mixture solutions were poured into a three-necked flask, and heated in a water bath at 60° C. for 24 h. The supernatant of the reacted sample was poured off, the sample was centrifuged, washed, and vacuum-dried at 60° C. for 12 hours. The above-mentioned dried samples were heated up to 400° C. at a rate of 5° C. / min under an Ar atmosphere, and kept at this temperature for 1 h. Then, the temperature was raised from 400 °C to 1000 °C at the same rate of 5 °C / min, and the calcination was maintained for 1 h. Cool naturally to obtain a Fe-N-C catalyst sample.
PUM
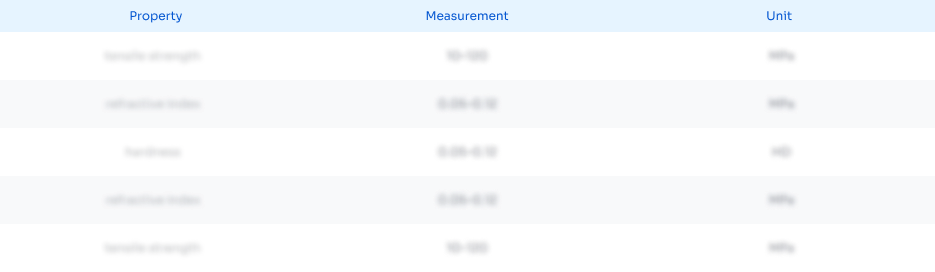
Abstract
Description
Claims
Application Information

- Generate Ideas
- Intellectual Property
- Life Sciences
- Materials
- Tech Scout
- Unparalleled Data Quality
- Higher Quality Content
- 60% Fewer Hallucinations
Browse by: Latest US Patents, China's latest patents, Technical Efficacy Thesaurus, Application Domain, Technology Topic, Popular Technical Reports.
© 2025 PatSnap. All rights reserved.Legal|Privacy policy|Modern Slavery Act Transparency Statement|Sitemap|About US| Contact US: help@patsnap.com