Differential-thickness rolling method for medium-thickness plate
A technology for steel plates and flat plates, applied in the field of medium and heavy plate production in the metallurgical industry, can solve problems such as uneven deformation and insufficient compression ratio, reduce rolling passes, increase reduction rate, and promote deformation to penetrate into the core of the rolled piece. Effect
- Summary
- Abstract
- Description
- Claims
- Application Information
AI Technical Summary
Problems solved by technology
Method used
Image
Examples
Embodiment Construction
[0013] Below in conjunction with accompanying drawing, the present invention will be further described by examples.
[0014] Refer to attached Figure 1-2 A differential thickness rolling method for medium and heavy plates, the number of passes of differential rolling is an even number, the first pass of differential rolling adopts the method of gradually increasing the reduction ratio, and the first pass of differential rolling is rolled out The thickness of the steel plate is different in the length direction, and the upper surface has a certain slope. The thinner end bites into the second pass of differential thickness rolling. The second pass of differential thickness rolling also adopts the method of gradually increasing the reduction rate. , the steel plate with a certain slope on the upper surface is rolled into a flat plate with the same thickness in the longitudinal direction, and so on, until the last pass of differential thickness rolling.
[0015] In this embodime...
PUM
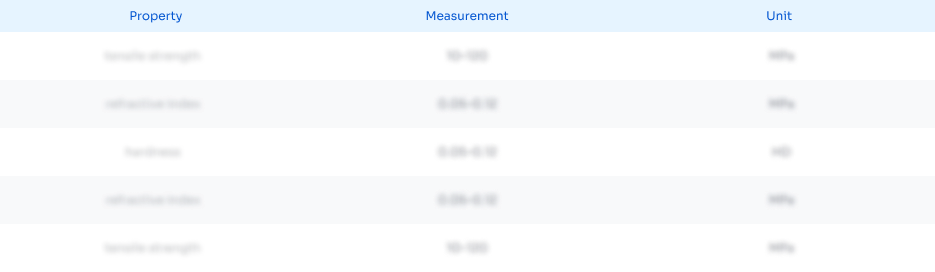
Abstract
Description
Claims
Application Information

- Generate Ideas
- Intellectual Property
- Life Sciences
- Materials
- Tech Scout
- Unparalleled Data Quality
- Higher Quality Content
- 60% Fewer Hallucinations
Browse by: Latest US Patents, China's latest patents, Technical Efficacy Thesaurus, Application Domain, Technology Topic, Popular Technical Reports.
© 2025 PatSnap. All rights reserved.Legal|Privacy policy|Modern Slavery Act Transparency Statement|Sitemap|About US| Contact US: help@patsnap.com