MgB2 superconducting cable joint and preparation and connection method thereof
A superconducting cable and superconducting technology, which are applied in the manufacturing of contacts, connecting contact materials, connecting/disconnecting of connecting devices, etc., can solve problems such as cable length limitation, reduce AC loss, simple manufacturing method, low AC The effect of loss
- Summary
- Abstract
- Description
- Claims
- Application Information
AI Technical Summary
Problems solved by technology
Method used
Image
Examples
Embodiment 1
[0026] The number of strands of the two superconducting cables to be connected is 3 strands, and all of them are superconducting strands. The specific implementation process is:
[0027] (1) In a vacuum glove box, fix the Mg rod in the middle of the Nb / Cu composite tube, and put the amorphous B powder into the gap between the Mg rod or the outside of the Mg tube and the Nb / Cu composite tube to obtain a Composite body; the atomic ratio of the Mg rod to the loaded B powder is 0.48-1. The outermost layer of the primary complex is Cu;
[0028] (2) Using 30% of the pass processing amount, the primary complex is drawn in multiple passes to a diameter of Φ5mm, and a 100mm length is cut off as a preform for making a superconducting joint. The specifications of each component in the cross section of the preform are determined by the center The areas outward are: the Mg area in the central area occupies the central area Φ2mm, the ring structure occupied by the B ring area is about Φ3....
Embodiment 2
[0037] The strands of the two superconducting cables to be connected are 3 strands and 4 strands respectively, and all of them are superconducting strands. The specific implementation process is:
[0038] (1) In a vacuum glove box, fix the Mg rod in the middle of the Nb / Cu composite tube, and put the amorphous B powder into the niobium-copper composite tube with the Mg rod in the middle to obtain a primary composite; the Mg rod and the filling The atomic ratio of the B powder is 0.48-1. The outermost layer of the primary complex is Cu;
[0039] (2) Using 20% of the pass processing amount, the primary complex is drawn in multiple passes to a diameter of Φ20mm, and the length of 200mm is intercepted as a preform for making a superconducting joint. The specifications of each component in the cross section of the preform are given by Outward from the central area are: the central area occupied by the Mg area is Φ8mm, the ring structure occupied by the B ring area is about Φ14×...
Embodiment 3
[0048] The number of strands of the two superconducting cables to be connected is 7 strands, and its structure is that 6 superconducting strands are evenly surrounded by 1 copper wire. The specific implementation process is:
[0049] (1) In the vacuum glove box, the Mg tube is fixed in the middle of the Nb / Cu composite tube, and the amorphous B powder is packed into the gap between the outside of the Mg tube and the Nb / Cu composite tube to obtain a primary complex; the Mg tube The atomic ratio to the loaded B powder is 0.48-1. The outermost layer of the primary complex is Cu;
[0050] (2) Using 10% of the pass processing amount, the primary complex is swaged or drawn to a diameter of Φ16mm, and a 100mm length is cut off as a preform for making a superconducting joint. The specifications to the outside are: the central area occupied by the Mg tube is a ring structure of about Φ8×4mm, the area occupied by the B ring area is about Φ12×8mm, and the area occupied by the Nb ring a...
PUM
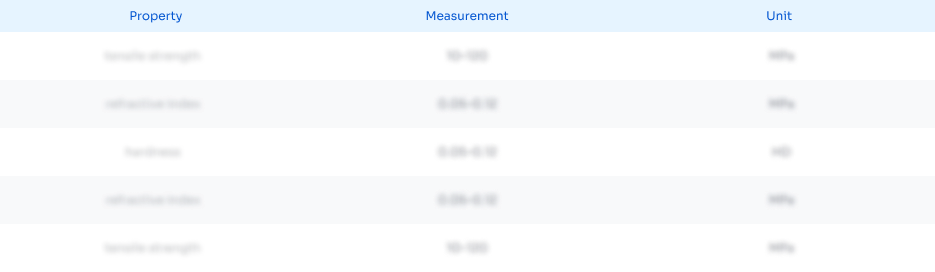
Abstract
Description
Claims
Application Information

- R&D Engineer
- R&D Manager
- IP Professional
- Industry Leading Data Capabilities
- Powerful AI technology
- Patent DNA Extraction
Browse by: Latest US Patents, China's latest patents, Technical Efficacy Thesaurus, Application Domain, Technology Topic, Popular Technical Reports.
© 2024 PatSnap. All rights reserved.Legal|Privacy policy|Modern Slavery Act Transparency Statement|Sitemap|About US| Contact US: help@patsnap.com