Mold for high-speed punching machine flywheel production
A high-speed punch and flywheel technology, applied in the field of molds for high-speed punch flywheel production, can solve the problems of low processing and molding efficiency, mold damage, and affecting the next use of the mold, so as to improve processing and molding efficiency, increase service life, and increase blowing range effect
- Summary
- Abstract
- Description
- Claims
- Application Information
AI Technical Summary
Problems solved by technology
Method used
Image
Examples
Embodiment 1
[0029] A mold for high-speed punch flywheel production, such as Figure 1-2 and Figure 5-6As shown, including the placement case 1, the left and right sides of the lower surface of the placement case 1 are fixedly connected with a support plate 2, and one side of the support plate 2 is fixedly connected with a heat dissipation mechanism 6, and the heat dissipation mechanism 6 includes a second motor 61. The left side of the second motor 61 is fixedly connected with the right side of the right support plate 2 through the connecting seat, the output shaft of the second motor 61 is fixedly connected with a cam 63, and the right end of the cam 63 is fitted with a moving plate 62, and the moving plate 62 The first slide bar 65 is fixedly connected to the left side of the left side, and the first slide bar 65 is slidably connected to the first slide sleeve that is clamped on one side of the right support plate 2. The outer surface of the first slide bar 65 is sleeved with A flexib...
Embodiment 2
[0032] A kind of high-speed press flywheel production mold, differs from embodiment 1 in that, as Figure 1-4 As shown, the left side of the upper surface of the support plate 2 is fixedly connected with a moving mechanism 3, the right side of the moving mechanism 3 is fixedly connected with a pressing mechanism 4, and the upper surface of the placement shell 1 is fixedly connected with two second slides. Rod 8, the outer surface of the second sliding rod 8 is provided with a second sliding sleeve, the connection shell 10 is fixedly connected between the two second sliding sleeves and the upper surface of the placement shell 1, and the moving mechanism 3 includes a fixed shell 36 and The first motor 31, wherein, the lower surface of the fixed shell 36 is fixedly connected with the upper surface of the placement shell 1, and the upper surface of the fixed shell 36 is fixedly connected with the left side of the first motor 31 through the fixing seat, and the first motor 31 The o...
Embodiment 3
[0035] A kind of high-speed press flywheel production mold, differs from embodiment 1 in that, as Figure 2-3 As shown, the connecting shell 10 is provided with a mold base 7, the connecting shell 10 is provided with a cleaning mechanism 5, the front of the connecting shell 10 is provided with a door, the cleaning mechanism 5 includes a fourth rotating shaft 57, and the fourth rotating shaft 57 The left and right sides of the outer surface are provided with fourth bearings, and the two fourth bearings are respectively clamped on the left and right sides of the inner wall of the connecting shell 10. One side of the fourth rotating shaft 57 is fixedly connected to one side of the mold base 7. The left side of the inner wall of the connecting shell 10 is fixedly connected with a mounting block 58 , and one side of the mounting block 58 is clipped with a second threaded post 59 , and one end of the second threaded post 59 is inserted into the limit position provided on one side of ...
PUM
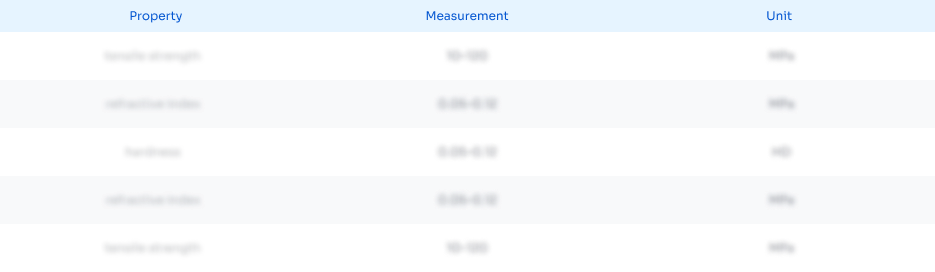
Abstract
Description
Claims
Application Information

- R&D
- Intellectual Property
- Life Sciences
- Materials
- Tech Scout
- Unparalleled Data Quality
- Higher Quality Content
- 60% Fewer Hallucinations
Browse by: Latest US Patents, China's latest patents, Technical Efficacy Thesaurus, Application Domain, Technology Topic, Popular Technical Reports.
© 2025 PatSnap. All rights reserved.Legal|Privacy policy|Modern Slavery Act Transparency Statement|Sitemap|About US| Contact US: help@patsnap.com