An intelligent support rod with high frequency response infinite stiffness based on semi-active control method
A support rod and high-frequency response technology, which is applied in the direction of vibration suppression adjustment, spring/shock absorber, mechanical equipment, etc., can solve the problems of large amount of interaction with the upper controller, large mass of support rod system truss, and complex system control loop. , to achieve the effects of not being affected by external temperature changes, compact structure, and small volume
- Summary
- Abstract
- Description
- Claims
- Application Information
AI Technical Summary
Problems solved by technology
Method used
Image
Examples
Embodiment Construction
[0021] The present invention will be further described in detail below with reference to the accompanying drawings and specific embodiments.
[0022] For the general two-force rods hinged at both ends, the commonly used support rod 1 and the series rod 2 made of electrostrictive material are installed in series in the present invention. The stress deformation of the commonly used strut member 1 is due to the fact that the strain measurement sensor group 3 consists of the first strain sensor 3-1, the second strain sensor 3-2, the third strain sensor 3-3, and the fourth strain sensor 3-4. A Wheatstone full-bridge strain circuit is formed to ensure that the measurement results are basically not affected by changes in the external temperature environment.
[0023] The high-integration analog controller 4 is installed in the miniature thermostatic control box 5, and is composed of a differential signal instrumentation amplifier 6, a high output impedance drive amplifier 7, and a po...
PUM
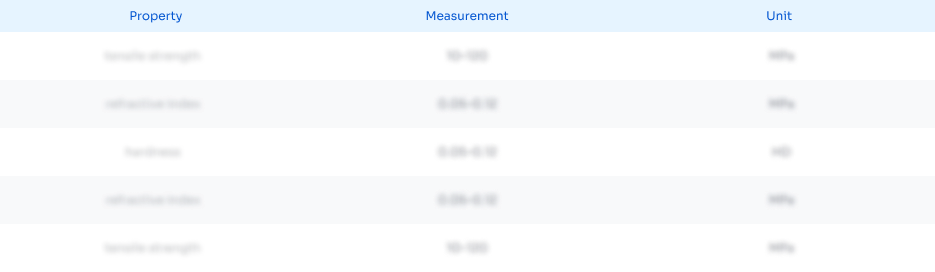
Abstract
Description
Claims
Application Information

- Generate Ideas
- Intellectual Property
- Life Sciences
- Materials
- Tech Scout
- Unparalleled Data Quality
- Higher Quality Content
- 60% Fewer Hallucinations
Browse by: Latest US Patents, China's latest patents, Technical Efficacy Thesaurus, Application Domain, Technology Topic, Popular Technical Reports.
© 2025 PatSnap. All rights reserved.Legal|Privacy policy|Modern Slavery Act Transparency Statement|Sitemap|About US| Contact US: help@patsnap.com