A surface treatment process for aluminum-magnesium alloy precision die-casting parts
An aluminum-magnesium alloy and surface treatment technology, applied in the field of die-casting preparation, can solve the problems of complex outer surface shape of die-casting, increase the labor intensity of workers, physical injury of workers, etc. The effect of work intensity
- Summary
- Abstract
- Description
- Claims
- Application Information
AI Technical Summary
Problems solved by technology
Method used
Image
Examples
Embodiment Construction
[0031] In order to make the technical problems, technical solutions and beneficial effects to be solved by the present invention clearer, the present invention will be described in further detail below in conjunction with the accompanying drawings and embodiments. It should be understood that the specific embodiments described here are only used to explain the present invention , and are not intended to limit the present invention.
[0032] Referring to 1-7, a surface treatment process for aluminum-magnesium alloy precision die-casting parts uses a surface treatment device for aluminum-magnesium alloy precision die-casting parts. The surface treatment device for aluminum-magnesium alloy precision die-casting parts includes a mounting base plate 1, a The column 2, the frame 3, the spray head 4, the conveying mechanism 5 and the cleaning mechanism 6, the specific process of using the above-mentioned aluminum-magnesium alloy precision die-casting surface treatment device for the s...
PUM
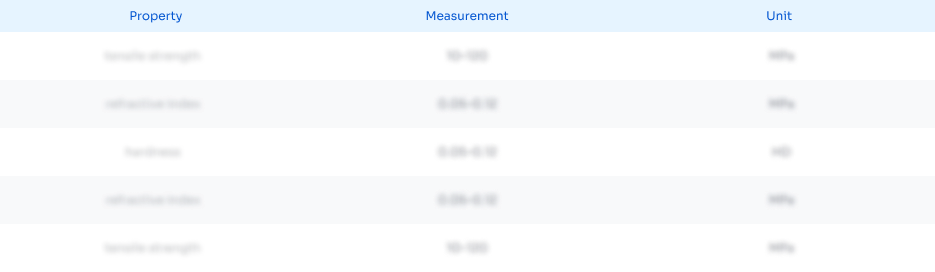
Abstract
Description
Claims
Application Information

- R&D
- Intellectual Property
- Life Sciences
- Materials
- Tech Scout
- Unparalleled Data Quality
- Higher Quality Content
- 60% Fewer Hallucinations
Browse by: Latest US Patents, China's latest patents, Technical Efficacy Thesaurus, Application Domain, Technology Topic, Popular Technical Reports.
© 2025 PatSnap. All rights reserved.Legal|Privacy policy|Modern Slavery Act Transparency Statement|Sitemap|About US| Contact US: help@patsnap.com