High-precision temperature measurement and control method based on double feedback
A high-precision, dual-feedback technology, used in radiation pyrometry, temperature control, measurement devices, etc., can solve problems such as weak design and analysis capabilities, unfavorable engineering operations, and lack of accuracy, and achieve improved anti-interference capabilities, The effect of meeting imaging quality requirements and reducing time and cost
- Summary
- Abstract
- Description
- Claims
- Application Information
AI Technical Summary
Problems solved by technology
Method used
Image
Examples
Embodiment Construction
[0052] The present invention will be further elaborated below in conjunction with embodiment.
[0053] Such as Figure 13 , the specific process is as follows:
[0054]The first step, temperature data acquisition: in the near-focus plane temperature precise measurement circuit, the constant current drive temperature measurement part completes the constant current drive of the temperature sensor; the data conditioning part completes the secondary amplification of the temperature data analog quantity; the analog-to-digital conversion Complete the analog-to-digital conversion and filtering of temperature data with the digital filtering part to form the main feedback digital temperature data; transmit it to the high-precision temperature control part through the secondary bus, and feed back to the model recognition part to complete the system model recognition.
[0055] At the same time, the refrigeration controller completes the transmission of the temperature data analog quanti...
PUM
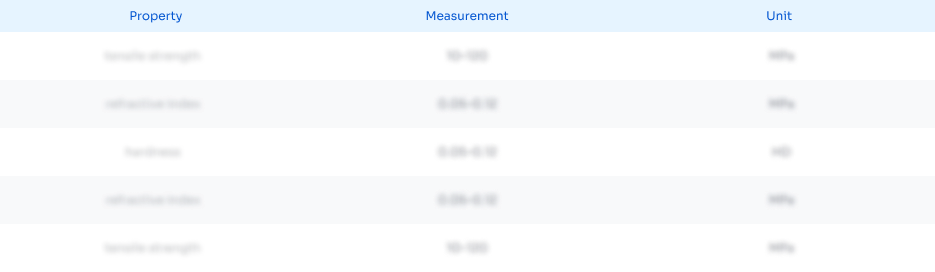
Abstract
Description
Claims
Application Information

- R&D
- Intellectual Property
- Life Sciences
- Materials
- Tech Scout
- Unparalleled Data Quality
- Higher Quality Content
- 60% Fewer Hallucinations
Browse by: Latest US Patents, China's latest patents, Technical Efficacy Thesaurus, Application Domain, Technology Topic, Popular Technical Reports.
© 2025 PatSnap. All rights reserved.Legal|Privacy policy|Modern Slavery Act Transparency Statement|Sitemap|About US| Contact US: help@patsnap.com