Gypsum powder production system and production process thereof
A production system and production process technology, applied in the field of building materials
- Summary
- Abstract
- Description
- Claims
- Application Information
AI Technical Summary
Problems solved by technology
Method used
Image
Examples
Embodiment 1
[0035] Such as figure 1 A gypsum powder production system shown includes a paddle dryer 1, a fluidized calciner 2, a vertical cooler 3, and a finished product bin 4. After the gypsum is first dried by the paddle dryer 1, it enters the fluid flow calcined in the calciner 2, then enters the vertical cooler 3 for cooling, and finally enters the finished product bin 4 after being pressed;
[0036] A feeding hopper 5 is installed at the feeding port of the fluidized calciner 2, and a grid heat exchanger 6 is installed in the feeding hopper 5, and the grid heat exchanger 6 passes through the vertical cooler 3 pipe connection;
[0037] The production system also includes a flash separator 7 and a calcining steam heat exchanger 8, the flash separator 7 is connected to the paddle dryer 1, the calcining steam heat exchanger 8 is connected to the fluidized calcining The machine 2 is connected; the secondary steam generated during the calcination process of the material in the fluidized...
Embodiment 2
[0048] A kind of gypsum powder production process, described production process adopts the production system described in embodiment 1, and described production process comprises the steps:
[0049] When the gypsum enters the feeding hopper 5, it is preheated by the grid heat exchanger 6, and then enters the paddle dryer 1 for drying; the condensed water generated in the paddle dryer 1 enters the In the drier condensate tank 11 of the production system;
[0050] The dried gypsum enters the fluidized calciner 2 for calcining, and the secondary steam generated during the calcining process of the material in the fluidized calciner 2 returns to the The paddle dryer 1 provides a supplementary drying heat source for the material. In order to make full use of the heat energy, a vacuum pump is used to evacuate the paddle dryer 1 with a vacuum degree of -20Kpa, and the paddle dryer 1 is vacuumed by the flash separator. The material in the inner chamber of the leaf dryer is flashed at ...
PUM
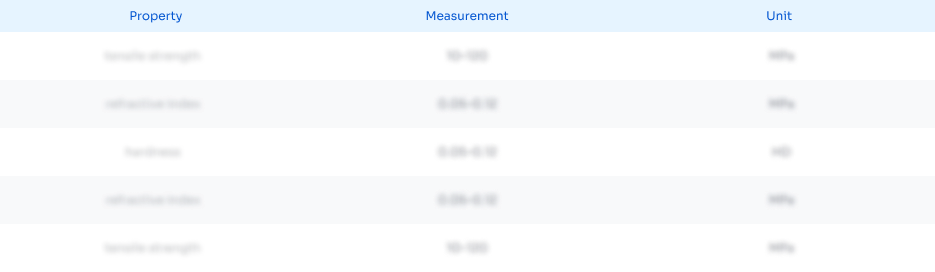
Abstract
Description
Claims
Application Information

- R&D Engineer
- R&D Manager
- IP Professional
- Industry Leading Data Capabilities
- Powerful AI technology
- Patent DNA Extraction
Browse by: Latest US Patents, China's latest patents, Technical Efficacy Thesaurus, Application Domain, Technology Topic, Popular Technical Reports.
© 2024 PatSnap. All rights reserved.Legal|Privacy policy|Modern Slavery Act Transparency Statement|Sitemap|About US| Contact US: help@patsnap.com