A rolling finishing method and processing device for hot-rolled steel
A rebar and trial processing technology, applied in the field of rebar hot rolling manufacturing rolling and finishing devices, can solve the problems of large occupied space, long equipment line, reduced production efficiency, etc., to prevent high temperature damage, shorten the overall length, The effect of improving processing efficiency
- Summary
- Abstract
- Description
- Claims
- Application Information
AI Technical Summary
Problems solved by technology
Method used
Image
Examples
Embodiment 1
[0048] Such as figure 1 As shown, a method for hot-rolled manufacturing and rolling finishing of threaded steel according to an embodiment of the present invention includes the following steps:
[0049] S1, heat treatment: put the round steel bar into the walking heating furnace for heating;
[0050] S2. Low-speed trial processing: send the round steel bar heated in S1 into the shell 5 at a low speed and undergo rough rolling, intermediate rolling, primary finishing rolling and secondary finishing rolling in sequence. The temperature of the round steel bar itself is dissipated to the shell 5. , so that the temperature inside the housing 5 increases;
[0051] S3, start the cooling mechanism: After completing the step S2, start the first blower 503 and the second blower 505, adjust the ratio of the mixed gas through the first proportional valve 514 and the second proportional valve 516, and mix the gas with different temperatures, and then Jet out from the oblique air holes 52...
PUM
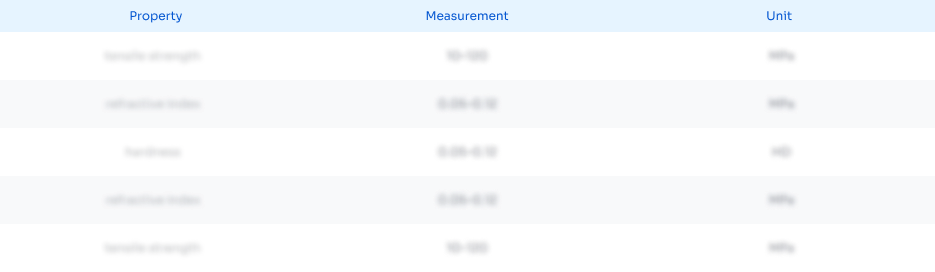
Abstract
Description
Claims
Application Information

- R&D
- Intellectual Property
- Life Sciences
- Materials
- Tech Scout
- Unparalleled Data Quality
- Higher Quality Content
- 60% Fewer Hallucinations
Browse by: Latest US Patents, China's latest patents, Technical Efficacy Thesaurus, Application Domain, Technology Topic, Popular Technical Reports.
© 2025 PatSnap. All rights reserved.Legal|Privacy policy|Modern Slavery Act Transparency Statement|Sitemap|About US| Contact US: help@patsnap.com