Current prediction control method of duplex winding induction generator system
A technology of induction generator and current prediction, applied in motor generator control, electronic commutation motor control, control generator and other directions, can solve the problem that the application of double-winding induction generator has not been studied, and achieve steady-state control performance Excellent, good current control performance, the effect of fixed switching frequency
- Summary
- Abstract
- Description
- Claims
- Application Information
AI Technical Summary
Problems solved by technology
Method used
Image
Examples
Embodiment Construction
[0051] The specific embodiments of the present invention will be further described below in conjunction with the accompanying drawings.
[0052] The schematic diagram of the five-phase two-winding induction generator system is as follows: figure 1 As shown, the control winding side of the five-phase double-winding induction generator is connected with a five-phase static excitation converter SEC, which is used to adjust the reactive power of the generator; the power winding side is connected with a DC load and a five-phase uncontrolled rectifier bridge. The electricity directly outputs DC power through a five-phase rectifier bridge.
[0053] In the five-phase double-winding induction generator system, the DC bus voltage on the control winding side is positively correlated with the electromagnetic torque, and the DC bus voltage on the power winding side is positively correlated with the flux linkage amplitude. The electromagnetic torque is adjusted by active power, and the qua...
PUM
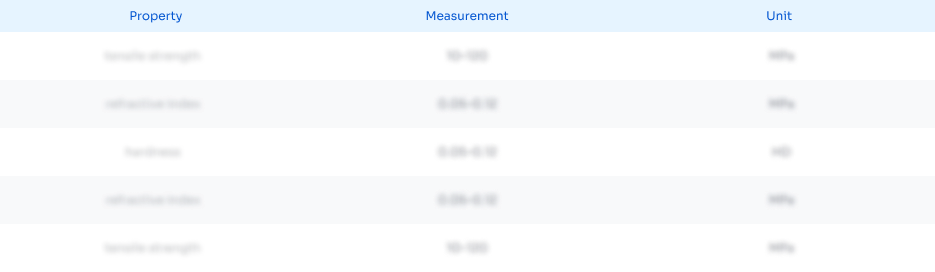
Abstract
Description
Claims
Application Information

- R&D
- Intellectual Property
- Life Sciences
- Materials
- Tech Scout
- Unparalleled Data Quality
- Higher Quality Content
- 60% Fewer Hallucinations
Browse by: Latest US Patents, China's latest patents, Technical Efficacy Thesaurus, Application Domain, Technology Topic, Popular Technical Reports.
© 2025 PatSnap. All rights reserved.Legal|Privacy policy|Modern Slavery Act Transparency Statement|Sitemap|About US| Contact US: help@patsnap.com