Multi-station numerical control bearing rolling machining system and method
A multi-station, bearing technology, used in bearing components, shafts and bearings, metal processing equipment, etc., can solve the problems of relative sliding of the shaft ring, uneven lubrication of the fixed groove, and inability to recover the lubricating fluid, so as to improve the lubrication Cooling effect, easy spraying, effect of avoiding clogging
- Summary
- Abstract
- Description
- Claims
- Application Information
AI Technical Summary
Problems solved by technology
Method used
Image
Examples
Embodiment
[0031] see Figure 1-Figure 6 , the present invention provides a multi-station numerical control bearing rolling processing system and method, the structure of which includes a top frame 1, a control panel 2, a rolling head 3, a connecting plate 4, a station fixing structure 5, a sliding bottom frame 6, Support feet 7, hydraulic rods 8, sliding grooves 9, the bottom of the sliding chassis 6 is provided with more than two supporting feet 7, a sliding groove 9 is opened in the middle of the sliding chassis 6 horizontally, and the sliding groove 9 A hydraulic rod 8 is installed at one end, and the end of the hydraulic cylinder 8 is connected and fixed with the station fixing structure 5. The top frame 1 is horizontally fixed on the side of the sliding bottom frame 6, and the top frame 1 and the side of the sliding bottom frame 6 are fixed with The connecting strap 4 is movably matched with the station fixing structure 5, and a rolling head 3 is installed on the top frame 1 direct...
PUM
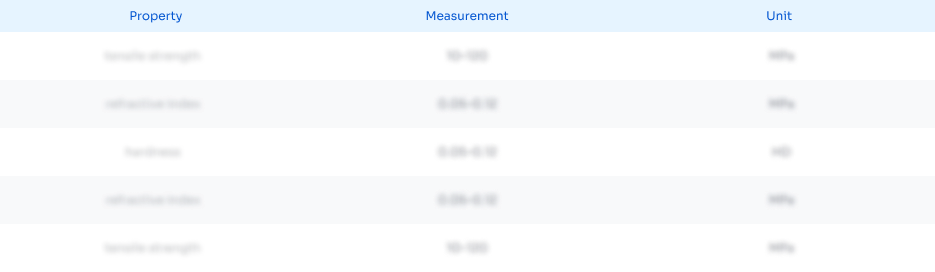
Abstract
Description
Claims
Application Information

- R&D
- Intellectual Property
- Life Sciences
- Materials
- Tech Scout
- Unparalleled Data Quality
- Higher Quality Content
- 60% Fewer Hallucinations
Browse by: Latest US Patents, China's latest patents, Technical Efficacy Thesaurus, Application Domain, Technology Topic, Popular Technical Reports.
© 2025 PatSnap. All rights reserved.Legal|Privacy policy|Modern Slavery Act Transparency Statement|Sitemap|About US| Contact US: help@patsnap.com