Preparation method and application of highly graphitized biomass-based porous nitrogen-doped carbon fiber material
A nitrogen-doped carbon fiber and graphitization technology, applied in the chemical field, can solve the problems of restricting the development of cotton fiber application and low performance
- Summary
- Abstract
- Description
- Claims
- Application Information
AI Technical Summary
Problems solved by technology
Method used
Image
Examples
Embodiment 1
[0030] 0.75 g of waste cotton fiber (CF) was placed in a solution of dimethylimidazole in dry methanol (45 mL) at room temperature. After soaking for 24 hours, mix 45mL of anhydrous methanol solution of zinc nitrate with the above and stir well. After soaking for 24 h, it was washed with anhydrous methanol and dried (60 °C) to obtain the Zn-MOF / CF composite. The composite material is placed in a tube furnace, and an inert gas (high-purity nitrogen or argon) is introduced as a protective gas. The tube furnace was heated at a rate of 5°C min -1 Raise the temperature to 800°C for 2h. After cooling down to room temperature, use 6mol L -1 Soak in HCl solution at 60°C for 24h. Subsequently, it was washed several times with ultrapure water until the pH of the washing solution was 7 (neutral). After drying, a partially graphitized nitrogen-doped porous carbon fiber material is obtained. There is an obvious Zn-MOF framework structure on the carbon fiber surface ( figure 2 ), th...
Embodiment 2
[0032] Waste cotton fibers were placed in a mixed solution of dimethylimidazole (0.821 g) in absolute methanol and absolute ethanol (40 mL, volume ratio 1:1). After soaking for several hours, mix 40mL of zinc nitrate in anhydrous methanol and anhydrous ethanol (volume ratio: 1:1) with it, and stir well. Stand still for 24 hours, take out the composite cotton fiber material and clean it with absolute ethanol. After drying, the Zn-MOF / CF composite material can be obtained. The composite material is placed in a tube furnace, and an inert gas (high-purity nitrogen or argon) is introduced as a protective gas. The tube furnace was heated at a rate of 5°C min -1 Raise the temperature to 800°C for 2h. After cooling down to room temperature, use 6mol L -1 Soak in HCl solution at 60°C for 24h. Subsequently, it was washed several times with ultrapure water until the pH of the washing solution was 7 (neutral). After drying, a partially graphitized nitrogen-doped porous carbon fiber ...
Embodiment 3
[0034]Discarded cotton fibers (0.75 g) were placed in a solution of dimethylimidazole (0.821 g) in anhydrous methanol (45 mL) at room temperature. After soaking for 24 hours, 45 mL of anhydrous methanol solution of 0.1 g of zinc nitrate was fully stirred and mixed with the above solution. After soaking for 24 h, it was washed with anhydrous methanol and dried (60 °C) to obtain the Zn-MOF / CF composite. The Zn-MOF / CF composite was placed in a mixed solution of dimethylimidazole (0.821 g) in absolute methanol and absolute ethanol (40 mL, volume ratio 1:1). After soaking for 24 hours, mix 40mL cobalt nitrate (1g) in anhydrous methanol and absolute ethanol mixed solution (1:1 volume ratio) with it, and stir well. Stand still for 24 hours, take out the composite cotton fiber material and clean it with absolute ethanol. After drying, the Co-MOF@Zn-MOF / CF composite material can be obtained. The composite material is placed in a tube furnace, and an inert gas (high-purity nitrogen o...
PUM
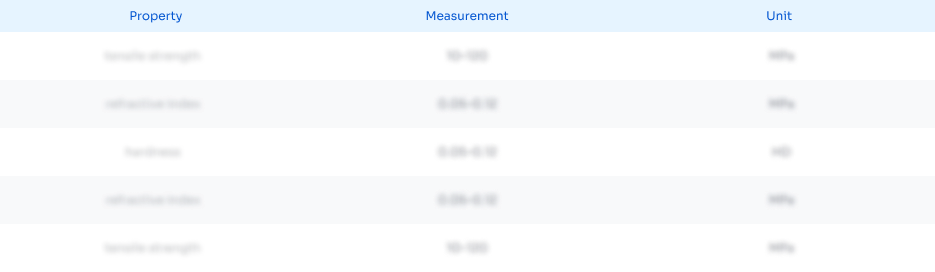
Abstract
Description
Claims
Application Information

- R&D
- Intellectual Property
- Life Sciences
- Materials
- Tech Scout
- Unparalleled Data Quality
- Higher Quality Content
- 60% Fewer Hallucinations
Browse by: Latest US Patents, China's latest patents, Technical Efficacy Thesaurus, Application Domain, Technology Topic, Popular Technical Reports.
© 2025 PatSnap. All rights reserved.Legal|Privacy policy|Modern Slavery Act Transparency Statement|Sitemap|About US| Contact US: help@patsnap.com