Non-contact sensor position adjusting structure for measuring shafts
A non-contact, structure-adjusting technology, applied in the direction of supporting machines, mechanical equipment, machine tables/supports, etc., can solve problems such as poor reliability, inaccurate measurement, and measurement failure
- Summary
- Abstract
- Description
- Claims
- Application Information
AI Technical Summary
Problems solved by technology
Method used
Image
Examples
Embodiment Construction
[0023] The technical solutions of the present invention will be further fully and clearly described below in conjunction with the accompanying drawings and specific embodiments.
[0024] Such as figure 1 As shown, the present invention includes the equipment measurement reference, and also includes a fixed assembly A0, a translation assembly B0 and a rotation assembly C0, the fixed assembly A0 is fixedly installed on the equipment measurement reference, and the translation assembly B0 can be adjusted up and down and fixed on the fixed assembly A0 , the rotation assembly C0 can be relatively rotatably installed on the translation assembly B0.
[0025] Such as figure 2 and image 3 As shown, the fixing assembly A0 includes a measuring mechanism base A1, a main body bracket A2 and a first screw A3. The measuring mechanism base A1 is fixedly installed on the equipment measurement reference, and the main body bracket A2 is fixedly installed on the measuring mechanism base A1.
...
PUM
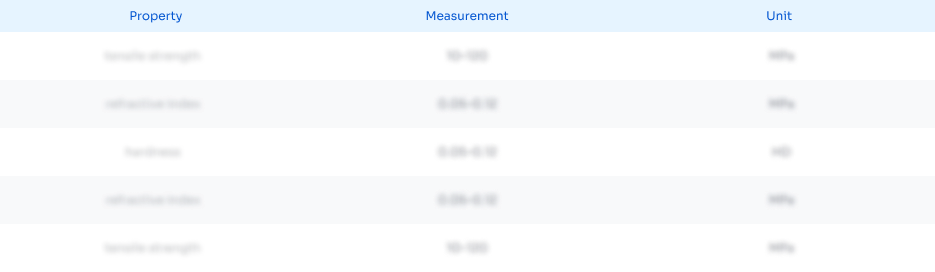
Abstract
Description
Claims
Application Information

- R&D
- Intellectual Property
- Life Sciences
- Materials
- Tech Scout
- Unparalleled Data Quality
- Higher Quality Content
- 60% Fewer Hallucinations
Browse by: Latest US Patents, China's latest patents, Technical Efficacy Thesaurus, Application Domain, Technology Topic, Popular Technical Reports.
© 2025 PatSnap. All rights reserved.Legal|Privacy policy|Modern Slavery Act Transparency Statement|Sitemap|About US| Contact US: help@patsnap.com