Method for continuously synthesizing 1H-1,2,3-triazole by using microchannel reactor
A microchannel reactor, 1H-1 technology, applied in chemical instruments and methods, chemistry/physics/physicochemical reactors, organic chemistry, etc., can solve problems such as potential safety hazards
- Summary
- Abstract
- Description
- Claims
- Application Information
AI Technical Summary
Problems solved by technology
Method used
Image
Examples
Embodiment 1
[0047]1) hydrazine hydrate aqueous solution (80%) 190g is delivered to preheating in the preheating module of microchannel reactor according to the flow rate of 40g / min, enters the first reaction module group of microchannel reactor after preheating, glyoxal Aqueous solution (40%) 200g is passed into the first reaction module by the flow velocity of 37.9g / min, and the first reaction module temperature is 100 ℃, and in the first reaction module, total residence time is 30s and hydrazine hydrate reacts, then in cooling The module was cooled to 30°C to obtain material 1;
[0048] 2) Material 1 continues to pass into the second reaction module, and at the same time, hydrogen peroxide solution (30%) is passed into the second reaction module at a flow rate of 32.6mL / min and undergoes oxidative cyclization reaction with material 1 at a reaction temperature of 30°C. The time is 30s, and the material 2 is obtained;
[0049] 3) Material 2 continues to pass into the third reaction modul...
Embodiment 2
[0053] 1) hydrazine hydrate aqueous solution (80%) 190g is delivered to preheating in the preheating module of microchannel reactor according to the flow rate of 40g / min, enters the first reaction module group of microchannel reactor after preheating, glyoxal Aqueous solution (40%) 200g is passed into the first reaction module by the flow rate of 40g / min, and the first reaction module temperature is 50 ℃, and in the first reaction module, total residence time is that 60s and hydrazine hydrate react, then in cooling module Cool down to 30°C to obtain material 1;
[0054] 2) Material 1 continues to pass into the second reaction module, and at the same time, hydrogen peroxide solution (30%) is passed into the second reaction module at a flow rate of 35mL / min to carry out oxidative cyclization reaction with material 1, the reaction temperature is 15°C, and the residence time Be 40s, make material 2;
[0055] 3) Material 2 continues to pass into the third reaction module of the mi...
Embodiment 3
[0059] 1) hydrazine hydrate aqueous solution (80%) 190g is delivered to preheating in the preheating module of microchannel reactor according to the flow rate of 40g / min, enters the first reaction module group of microchannel reactor after preheating, glyoxal Aqueous solution (40%) 200g passes into the first reaction module by the flow velocity of 35g / min, and the first reaction module temperature is 80 ℃, and in the first reaction module, total residence time is 42s and hydrazine hydrate reacts, then in cooling module Cool down to 35°C to obtain material 1;
[0060] 2) Material 1 continues to pass into the second reaction module, and at the same time, hydrogen peroxide solution (30%) is passed into the second reaction module at a flow rate of 39mL / min and undergoes oxidative cyclization reaction with material 1, the reaction temperature is 35 ° C, the residence time Be 30s, make material 2;
[0061] 3) material 2 continues to pass into the third reaction module of the microc...
PUM
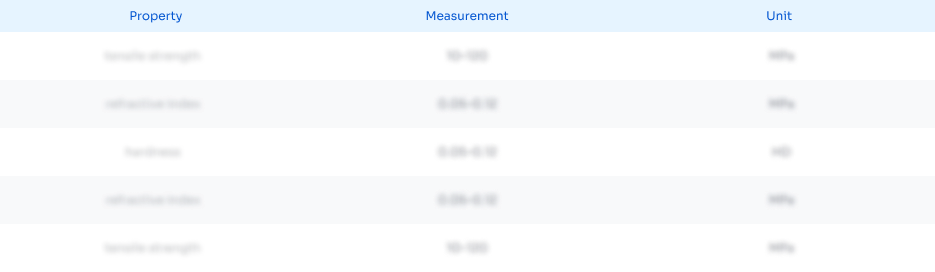
Abstract
Description
Claims
Application Information

- R&D
- Intellectual Property
- Life Sciences
- Materials
- Tech Scout
- Unparalleled Data Quality
- Higher Quality Content
- 60% Fewer Hallucinations
Browse by: Latest US Patents, China's latest patents, Technical Efficacy Thesaurus, Application Domain, Technology Topic, Popular Technical Reports.
© 2025 PatSnap. All rights reserved.Legal|Privacy policy|Modern Slavery Act Transparency Statement|Sitemap|About US| Contact US: help@patsnap.com