Inter-axle differential assembly for automobile through type drive axle and roller pin group thereof
An inter-axle differential and through-type technology, which is applied in the direction of differential transmission, transmission, transmission parts, etc., can solve the problems of high requirements for lubrication conditions, poor carrying capacity, and high maintenance costs, so as to improve the carrying capacity, Effect of improving load carrying capacity and reducing friction loss
- Summary
- Abstract
- Description
- Claims
- Application Information
AI Technical Summary
Problems solved by technology
Method used
Image
Examples
Embodiment 1
[0032] Such as figure 1 As shown, an inter-axle differential assembly for a through drive axle of an automobile includes a main shaft 11, a cross shaft 2 coaxially assembled outside the main shaft 11 through splines, a driving cylindrical gear 3, and four planetary gears. The gear 6 and the side gear 4, the driving cylindrical gear 3 and the side gear 4 are respectively coaxially and rotatably assembled at the front and rear ends of the main shaft 11, and the four planetary gears 6 are respectively coaxially assembled on the cross shaft 2 On the corresponding sub-shaft, and the front end of each planetary gear 6 is meshed with the driving cylindrical gear 3, and the rear end of each planetary gear 6 is meshed with the side gear 4, and each planetary gear 6 is internally A stepped hole 13 is provided, and the four sub-shafts of the cross shaft 2 are all inserted into the corresponding stepped holes 13, and the gap between the cross shaft 2 and the inner wall of the stepped hole...
Embodiment 2
[0041] Such as figure 2 As shown, a needle roller set 14 applied to the above-mentioned inter-axle differential assembly includes a circle of needle rollers 7, soft inner fittings 15 and soft outer fittings 16 prefabricated on the inner and outer rings of the needle rollers 7, so that The needle rollers 7 are evenly distributed between the inner fitting 15 and the outer fitting 16 through extrusion.
[0042] Specifically, the lengths of the inner assembly 15 and the outer assembly 16 are both shorter than the needle roller 7, and the end of the outer assembly 16 opposite to the initial press-in end of the needle roller group is shorter than the end of the needle roller 7, and the inner assembly 15 and the The opposite end of the initial press-in end of the cross shaft 2 is shorter than the end of the needle roller 7 .
Embodiment 3
[0044] A method for installing needle rollers at a cross shaft in an inter-axle differential assembly, comprising the following steps:
[0045]Step 1. Prefabricate a circle of soft inner fittings 15 and soft outer fittings 16 on the inner and outer rings of the needle roller 7, so that the needle rollers 7 are evenly distributed between the inner fittings 15 and the outer fittings 16, and ensure that the inner fittings 15 and The length of the external assembly 16 is shorter than that of the needle roller 7, the end of the external assembly 16 opposite to the initial press-in end of the needle roller group is shorter than the end of the needle roller 7, and the end of the internal assembly 15 opposite to the initial press-in end of the cross shaft 2 is shorter than the needle roller 7 ends, finally forming the needle roller group 14;
[0046] Step 2. Press the above-mentioned needle roller set 14 into the stepped hole 13 of the planetary gear 6, and then take out the outer ass...
PUM
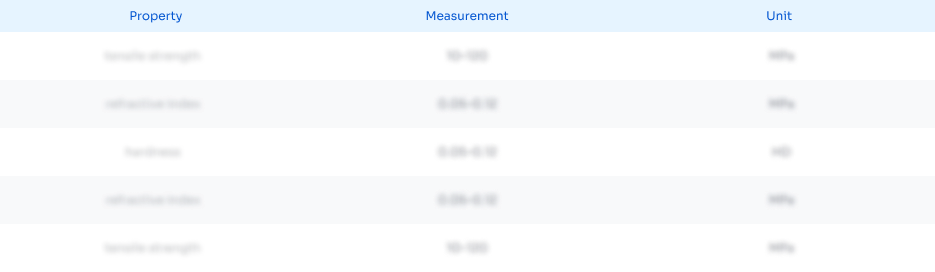
Abstract
Description
Claims
Application Information

- R&D Engineer
- R&D Manager
- IP Professional
- Industry Leading Data Capabilities
- Powerful AI technology
- Patent DNA Extraction
Browse by: Latest US Patents, China's latest patents, Technical Efficacy Thesaurus, Application Domain, Technology Topic, Popular Technical Reports.
© 2024 PatSnap. All rights reserved.Legal|Privacy policy|Modern Slavery Act Transparency Statement|Sitemap|About US| Contact US: help@patsnap.com