Metalloporphyrin terephthalate photo-thermal cellulose as well as preparation method and application thereof
A technology of terephthalate and terephthalic acid, which is applied in the field of antibacterial material preparation and can solve the problems that functional cellulose has not been reported.
- Summary
- Abstract
- Description
- Claims
- Application Information
AI Technical Summary
Problems solved by technology
Method used
Image
Examples
Embodiment 1
[0030] Example 1 (the optimal preparation scheme of CMF@PCNCu): the leaves of Chlorophytum chinensis were washed, chopped and dried. Weigh 2g of Chlorophytum leaf fragments and immerse in NaOH (150mL, 5wt%) aqueous solution and reflux at 70°C for 4h to remove lignin and other impurities in the cellulose. After the reaction, the cellulose was washed with deionized water and ethanol until the solution was neutral. The treated cellulose was immersed in NaClO 2 solution (150 mL, 2 wt%), refluxed at 60° C. for 3 h and cooled to room temperature. The cellulose in the solution was washed with deionized water and ethanol several times, and then dried in a forced air drying oven at 60°C.
[0031] In 20 mL, add 10 μmol of cellulose extracted from Chlorophytum leaves, 600 μmol of terephthalic acid and 800 μmol of sodium hypophosphite (the molar ratio of cellulose to terephthalic acid is 1:60; the molar ratio of cellulose to sodium hypophosphite is 1:80), stirred for the first time in ...
Embodiment 2
[0032] Embodiment 2: Wash and chop the leaves of Chlorophytum orchids and dry them. Weigh 2g of Chlorophytum leaf fragments and immerse in NaOH (150mL, 5wt%) aqueous solution and reflux at 70°C for 4h to remove lignin and other impurities in the cellulose. After the reaction, the cellulose was washed with deionized water and ethanol until the solution was neutral. The treated cellulose was immersed in NaClO 2 solution (150 mL, 2 wt%), refluxed at 60° C. for 3 h and cooled to room temperature. The cellulose in the solution was washed with deionized water and ethanol several times, and then dried in a forced air drying oven at 60°C.
[0033] In 20 mL, add 10 μmol of cellulose extracted from Chlorophytum leaves, 200 μmol of terephthalic acid and 800 μmol of sodium hypophosphite (the molar ratio of cellulose to terephthalic acid is 1:20; the molar ratio of cellulose to sodium hypophosphite is 1:80), stirred for the first time in an oil bath at 140°C for 8h to carry out esterifi...
Embodiment 3
[0034] Embodiment 3: Wash and chop the leaves of Chlorophytum orchids and dry them. Weigh 2g of Chlorophytum leaf fragments and immerse in NaOH (150mL, 5wt%) aqueous solution and reflux at 70°C for 4h to remove lignin and other impurities in the cellulose. After the reaction, the cellulose was washed with deionized water and ethanol until the solution was neutral. The treated cellulose was immersed in NaClO 2 solution (150 mL, 2 wt%), refluxed at 60° C. for 3 h and cooled to room temperature. The cellulose in the solution was washed with deionized water and ethanol several times, and then dried in a forced air drying oven at 60°C.
[0035] In 20 mL, add 10 μmol of cellulose extracted from Chlorophytum leaves, 600 μmol of terephthalic acid and 800 μmol of sodium hypophosphite (the molar ratio of cellulose to terephthalic acid is 1:60; the molar ratio of cellulose to sodium hypophosphite is 1:80), stirred for the first time in 140 ℃ oil bath for 8h to carry out esterification...
PUM
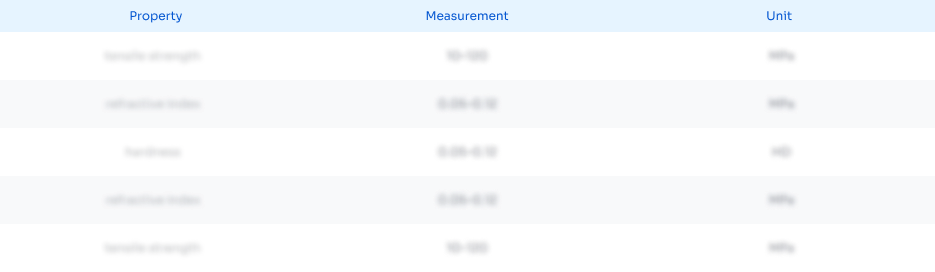
Abstract
Description
Claims
Application Information

- R&D Engineer
- R&D Manager
- IP Professional
- Industry Leading Data Capabilities
- Powerful AI technology
- Patent DNA Extraction
Browse by: Latest US Patents, China's latest patents, Technical Efficacy Thesaurus, Application Domain, Technology Topic.
© 2024 PatSnap. All rights reserved.Legal|Privacy policy|Modern Slavery Act Transparency Statement|Sitemap